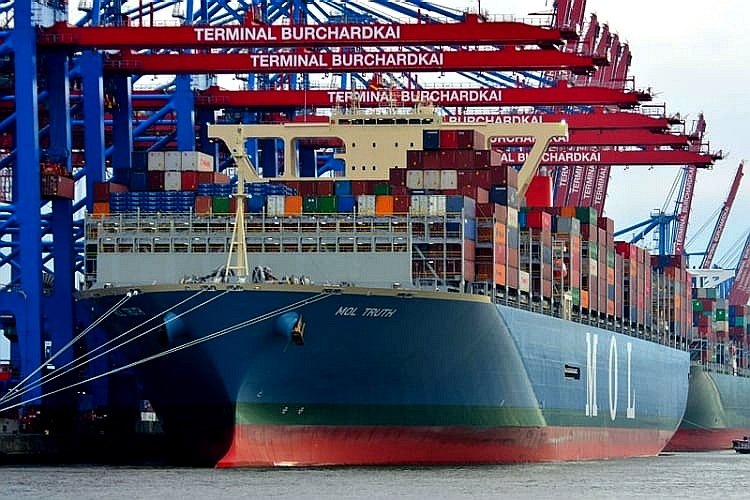
WE
NEED MORE EFFICIENT PORTS - Transportation is a commodity. The only real factors for customers to consider are cost and time. Of course, you have to assume that in either case your goods will arrive safely, but any part of the logistics chain that can’t handle the freight without damage won’t stay in business for long.
If
we are to attempt a world circumnavigation
in unmanned mode,
to include stops at various locations for media opportunities, the Elizabeth
Swann must be able dock or anchor autonomously - and interact with
the port authority or berthing operators.
If
this is to include multiple locations, or locations with auto-docking
facilities (for larger commercial vessels), then these locations will
need to be mapped, such that incoming vessels recognize the port and
know what the special docking arrangements are for autonomous vessels - if any.
Ports without such facilities may be identified and so avoided by
carriers operating ships that need a faster turn-around time.
The
reason that this is so important for clean ships of the future, is to do
with the practical constraints of a solar/wind powered cargo ship. It is
likely that such commercial vessels will be around a quarter the
capacity of
the, at present, 200,000 ton, 400 meter behemoths, according to a brief
overview by the Cleaner
Ocean Foundation in 2019.
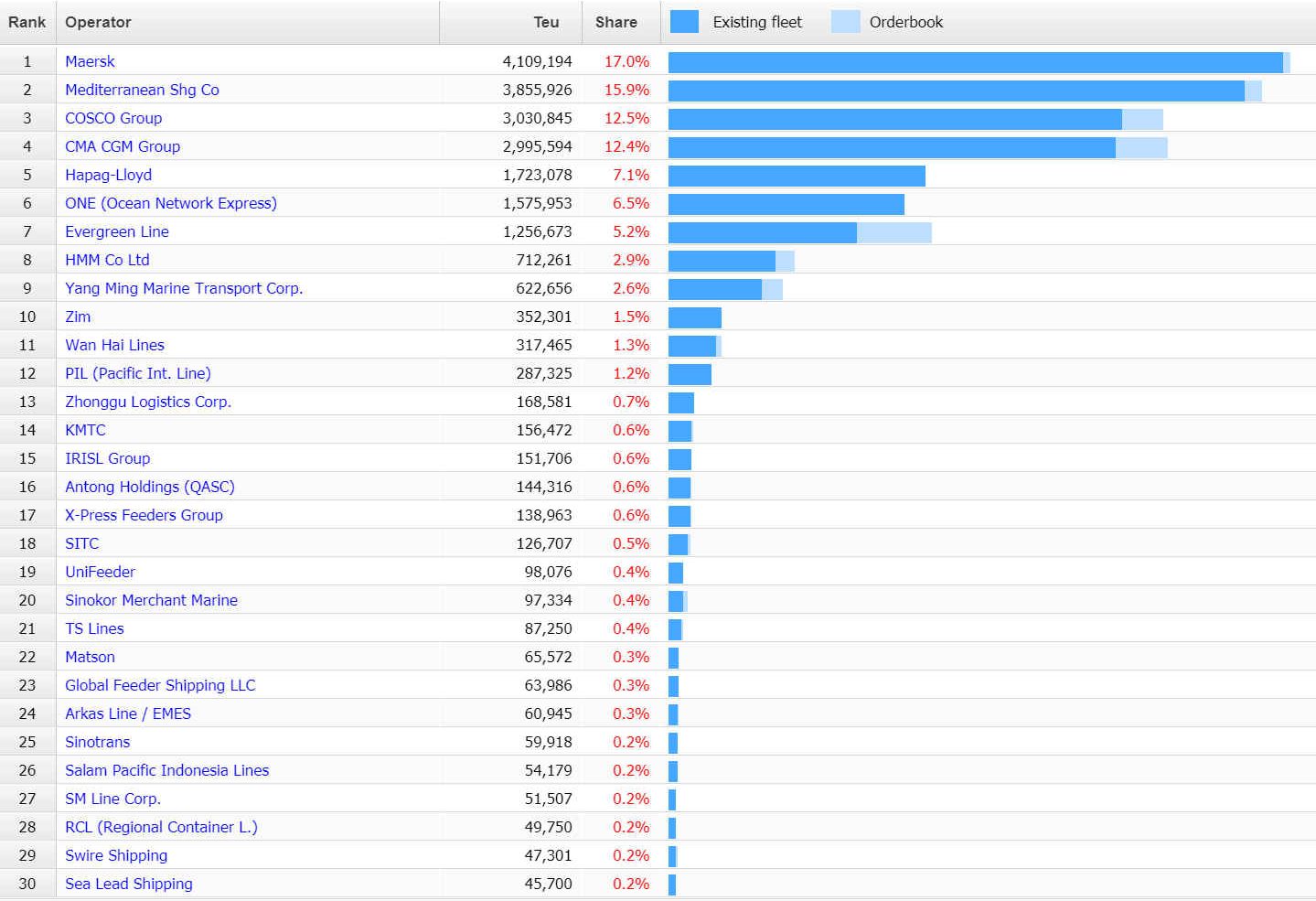
This
of course needs further study, but as a baseline assumption, and just to
begin conceptualizing the ports of the future, the docking, unloading,
loading and casting off, will need to be at least four times faster than
at present - to cope with the same level of international trade as we
presently enjoy. We stress, this is if shipping is solar and wind
powered - and that vision, also needs to be qualified/quantified by further study.
It
could be that zero emission (solar) ships have even lesser capacity, in
which case ports would need to be able to turnaround inbound ships even
more quickly. We'd imagine a worst case scenario of 10 times the present
turnaround time, meaning a rethink of port design that port and harbour
authorities may not like to think about right now. Or, at least the
change in technology will require a re-write of the rules of the road in
busy ports and harbours. Maybe even legislation by the IMO.
This
is all far ahead of current thinking, where fleet operators are more
concerned with immediate upgrades of existing assets, mainly focused on
cleaning up their dirty diesel engines. This is just to keep them in
business; a necessity, if the world is not to come to a virtual
standstill (as with Covid19)
and return to Victorian times.
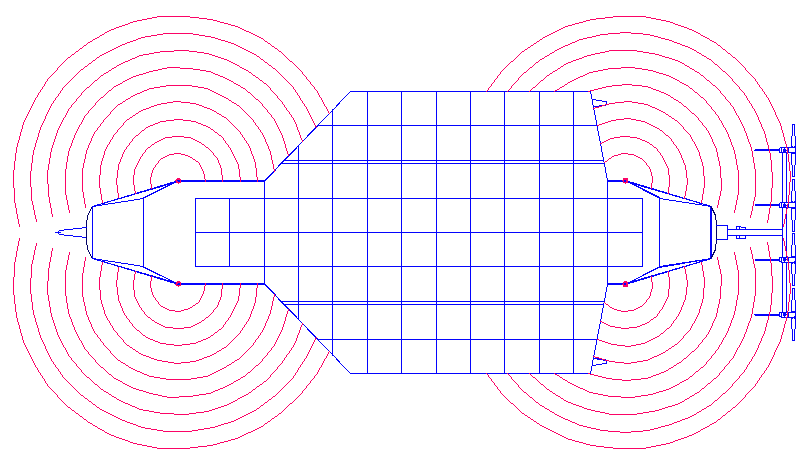
PUBLIC
RELATIONS - Suggested sensor locations on the Elizabeth Swann, to
allow autonomous docking for media opportunities, where the press and
public might enjoy a visit to their location by a fully autonomous
vessel. The vessel might interact with visitors to any docking station
via 'Skype,' 'Teams' or 'Zoom' type applications - linking dockside
visitors to the Crew anywhere in
the world. You can help us to make this world first happen, by
supporting the project.
We
owe it to the merchant navies of the world to give them advance warning
of possibly new technology, that they may make an informed choice in the
ordering and build of new ships that are profitable and meet the IMO's targets for
2050.
An
individual nation's fleet and the people that crew it (manned at present) are
referred to as its merchant navy. Merchant shipping is the lifeblood of
the world economy, carrying 90% of international trade many times more
efficiently than by road. For this reason,
it is vital to plan ahead, rather then try to patch up inadequate
facilities with sticky-tape, at a later date.
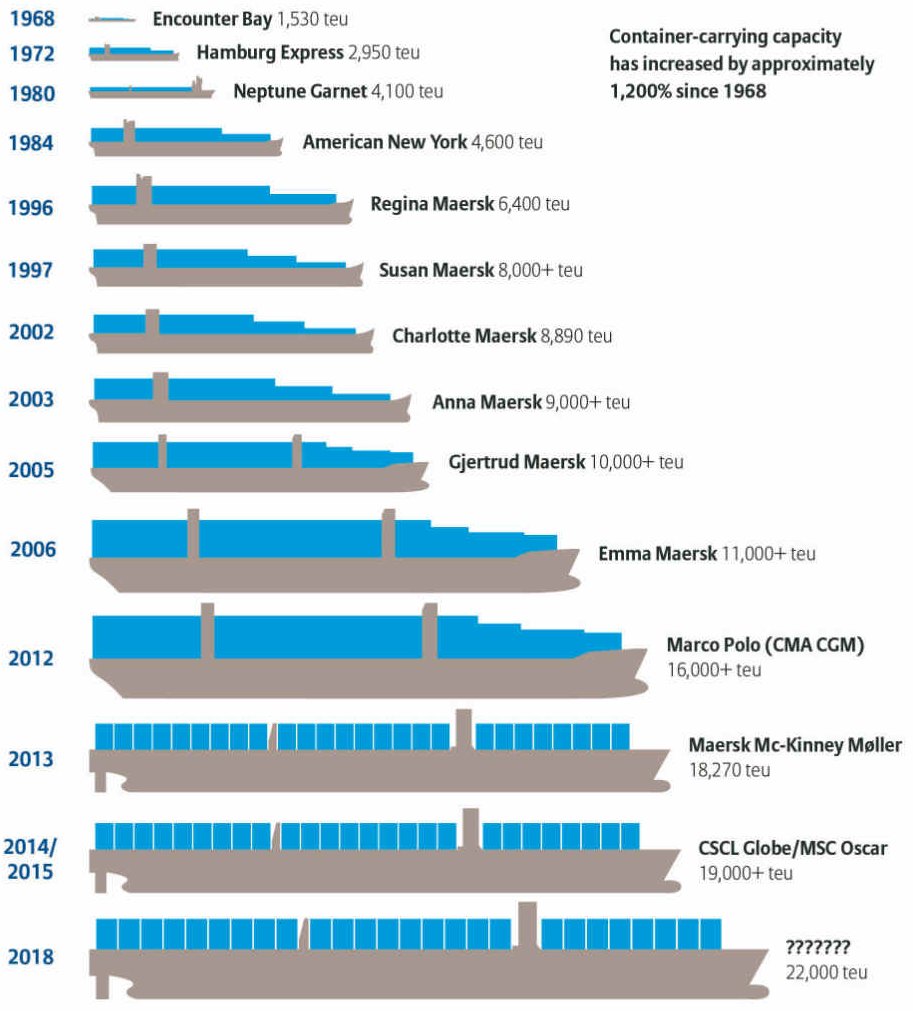

Projects
like the Elizabeth
Swann are the lifeblood of innovation. In any circumnavigation,
the autonomous docking experience, or lack of it, may serve to
underscore the state of port destinations - by way of a wake up call.
Unfortunately, there is no funding mechanism for SMEs
with such ambitions, hence we have a creative
campaign to draw attention to the project, and potentially secure
the support we need from like minded creative companies and commercial
risk share partners.
We
hope this information has been helpful.
CROSS
CHANNEL FERRY OPERATORS & ISLAND SERVICES
BRITTANY
FERRIES -
DFDS -
HOVERSPEED -
STENALINE -
P&O
FERRIES -
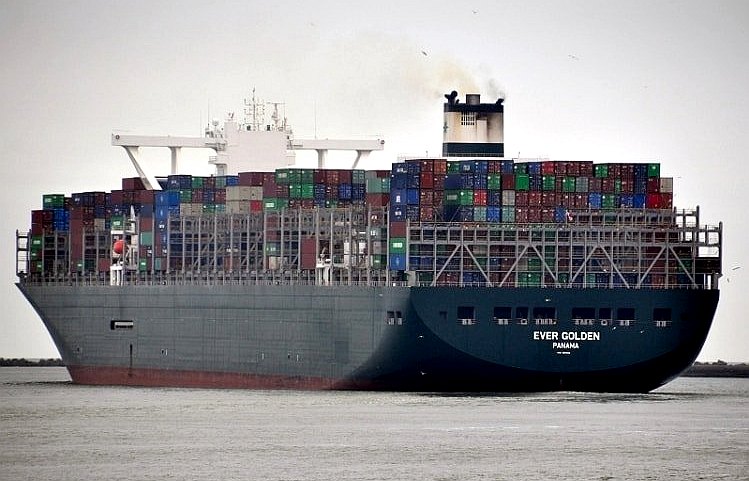
DINOSAURS -
As the shipping industry continues to face the challenges of globalization and
the increasing scale and utilization of vessels to deliver goods around
the world, we must continuously look for ways to improve efficiencies. Shipping companies and port operators must look for smarter ways to deliver against these expectations.
Solar powered ships might only achieve the required power to weight
ratio and ease of unloading using the technology developed for the
Elizabeth Swann. Why not help us to prove or disprove the theory by
supporting us on our quest to raise the blue-water speed record for
energy autonomous ships.
A-Z
INDEX OF H2 POWERED FUEL
CELL SHIP PROJECTS
BOREAL
SJO
FCS
ALTERWASSER
HYSEAS
III
NORLED
SAN
FRANCISCO BAY
SANDIA
& DNV-GL
SCANDLINES
VIKING
LINE
RANK
|
SHIP
NAME
|
No.
BUILT |
LOA,
Mtrs
|
TEU
|
DWT
|
|
|
|
|
|
|
1.
|
MSC
GULSUN
|
5 |
399.9
|
23,756
|
228,149
|
2.
|
OOCL
HONG KONG
|
5 |
399.9
|
21,413
|
197,317
|
3.
|
COSCO
Shipping Universe
|
3 |
400.0
|
21,237
|
198,485
|
4.
|
CMA
CGM Antoine
de Saint Exupery
|
2 |
400.0
|
20,954
|
199,855
|
5.
|
Madrid
MAERSK
|
10 |
399.0
|
20,568
|
210,019
|
6.
|
Ever
Golden
|
10 |
400.0
|
20,388
|
218,000
|
7.
|
MOL
Truth
|
1 |
399.0
|
20,182
|
189,766
|
8.
|
MOL
Triumph
|
3 |
400.0
|
20,170
|
192,672
|
9.
|
COSCO
Shipping Taurus
|
4 |
399.8
|
20,119
|
201,868
|
10.
|
Barzan
|
5 |
400.0
|
19,870
|
199,744
|
The
Cleaner Ocean Foundation
(COF) acts as a strategic thought provoking organization, with the objective of helping
shape the transport policy agenda on a global level and ensuring that it contributes to
economic stability, environmental protection, and the preservation of human life and well-being.
Unlike other bodies that provide such input, COF typically projects a
vision of a better future, not normally suggested by date alone.
It appears that ports do not systematically reports ship turnaround times.
Research thus remains hampered by missing information on loading time efficiency itself.
Information is typically based on time in port.
Turnaround time includes the time spent with entering the port, loading, unloading, and departing. Even though this is highly relevant for shipping lines [in terms of related port costs], ports do not
routinely present report turnaround times in annual reports or other publications.
Considering the importance of ocean transport internationally, the
inclusion of a systematic and comparative study on vessel turnaround times in
ports would aid transparency. Autonomous docking and AI geospatial data
analytics could provide a tool to develop port efficiency.
The average turnaround time illustrates the capability of the port to efficiently handle cargo
flows at the terminals and beyond. It can be defined as the average time a vessel needs to
stay in a port (difference between time of entrance and time of departure).Port calls and port turnaround times
According to UNCTAD, containerships have the lowest turnaround times. In 2018, a given ship spent a median of 23.5 hours in ports, i.e. 0.97 days. Dry bulk carriers spent typically 2.05 days during a port call, while container ships spent on average the least amount of time (0.7 days). Performances ranged between 0.23 days in the Faroe Islands and six and a half days in the Maldives.
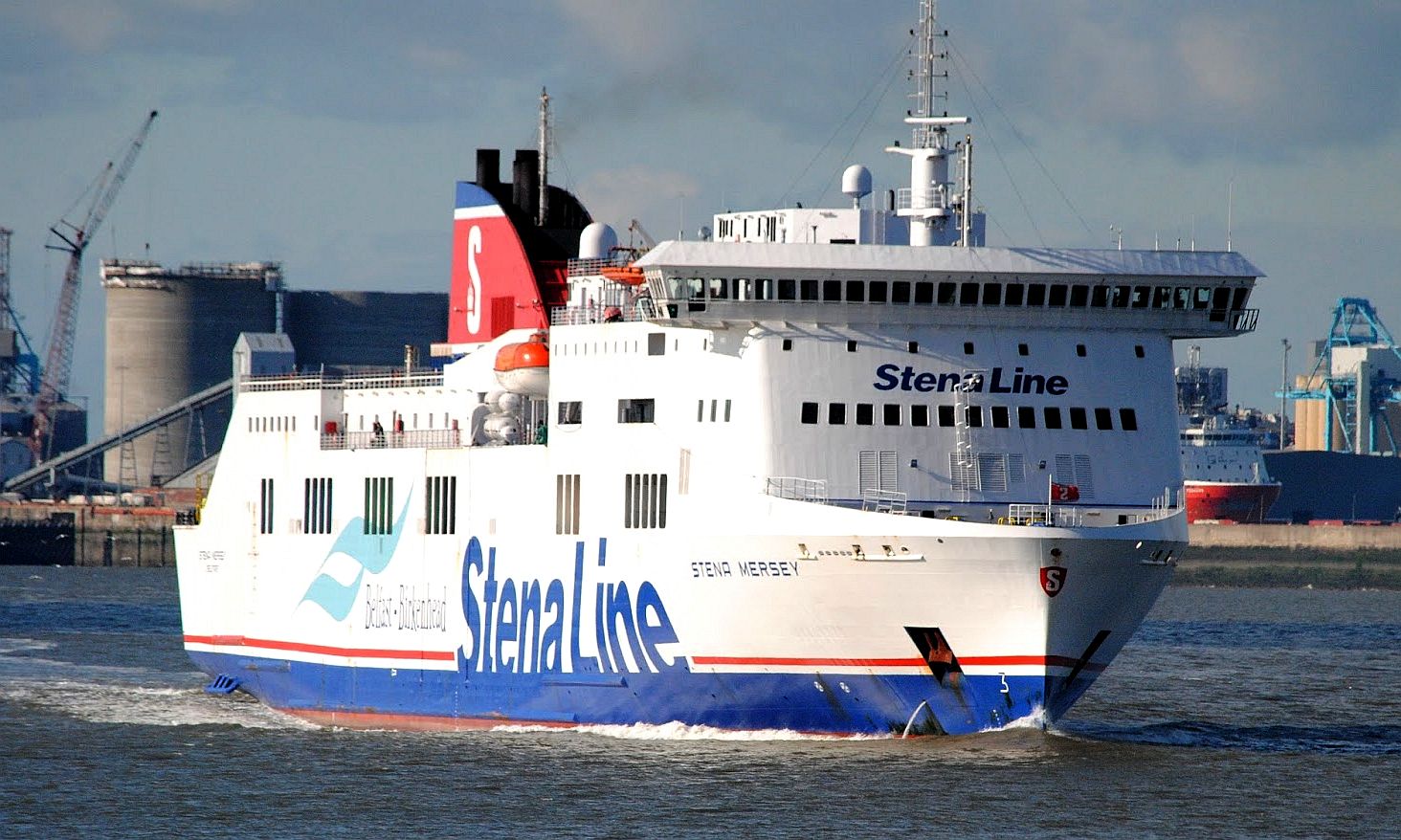
SMALLER
SHIPS FOR FASTER TURNAROUND
Considering
the lift height of containers from deck to dock, the time for each transport
might be reduced by the distance traveled x the time saved x the number
of containers. This would have to be balanced against docking and
undocking, assuming that port traffic control could cope with the
additional number of ships entering and leaving their system.
Automated
fast docking is a game changer, with docking reduced to minutes instead
of hours, smaller solar powered vessels begin to look attractive in
terms of ROI. Especially when fuel costs are factored in.
Indeed,
it may seem like financial madness to consider anything else. But this
all hangs on whether 10 knots or very close to can be achieved by solar
powered ships.
UNITED
NATIONS CONFERENCE on TRADE AND DEVELOPMENT - UNCTAD
What can be done to improve a port’s connectivity? The following seven policy measures
were considered key to enhancing port connectivity by UNCTAD:
1. Go digital. Digital and physical connectivity go hand in hand. Just as trade benefits from the latest technologies such as artificial intelligence, the Internet of Things and blockchain, port and shipping operations would also benefit from taping the opportunities arising from digitalization.
2. Link regional and global networks. Restrictions affecting regional or domestic cabotage markets limit the ability of shipping lines to consolidate cargo. Allowing international lines to also carry domestic trade and
feeder-ing cargo can enhance both the competitiveness of the port and shippers’ access to overseas markets.
3. Ensure competition. Considered prior analysis is required before assigning port concessions to terminal operators who are associated with shipping lines through vertical integration. On the one hand, such operators can attract port calls from associated lines and alliances. On the other, however, such vertical integration could discourage other lines from calling at the port and could limit choices available to shippers.
4. Port modernization. Port clients, i.e. the shipping lines and the traders, require fast, reliable and cost-efficient services to ships and cargo. Ports need to continuously invest in their technological, institutional and human capacities. Public and private cooperation is key in this regard.
5. Widen the hinterland. Ports should aim at attracting cargo from neighbouring countries and domestic production centres. There is a common interest between many seaports and traders in neighbouring countries, especially landlocked countries. Investments in corridors, regional trucking markets, and cross-border trade and transit facilitation can help expand ports’ hinterlands.
6. Promote sustainability. Port stakeholders are varied and may include shipping lines and traders, as well as social partners and the port-city community. Stakeholders are increasingly demanding that ports deliver on their social, economic and environmental sustainability obligations.
7. Monitor ports’ connectivity. Policy makers, port authorities and investors need to continuously monitor trends in the global shipping network, the geography of trade, fleet deployment, and port performance. UNCTAD’s Review of Maritime Transport and the complementary online statistical information and country profiles support this monitoring objective.
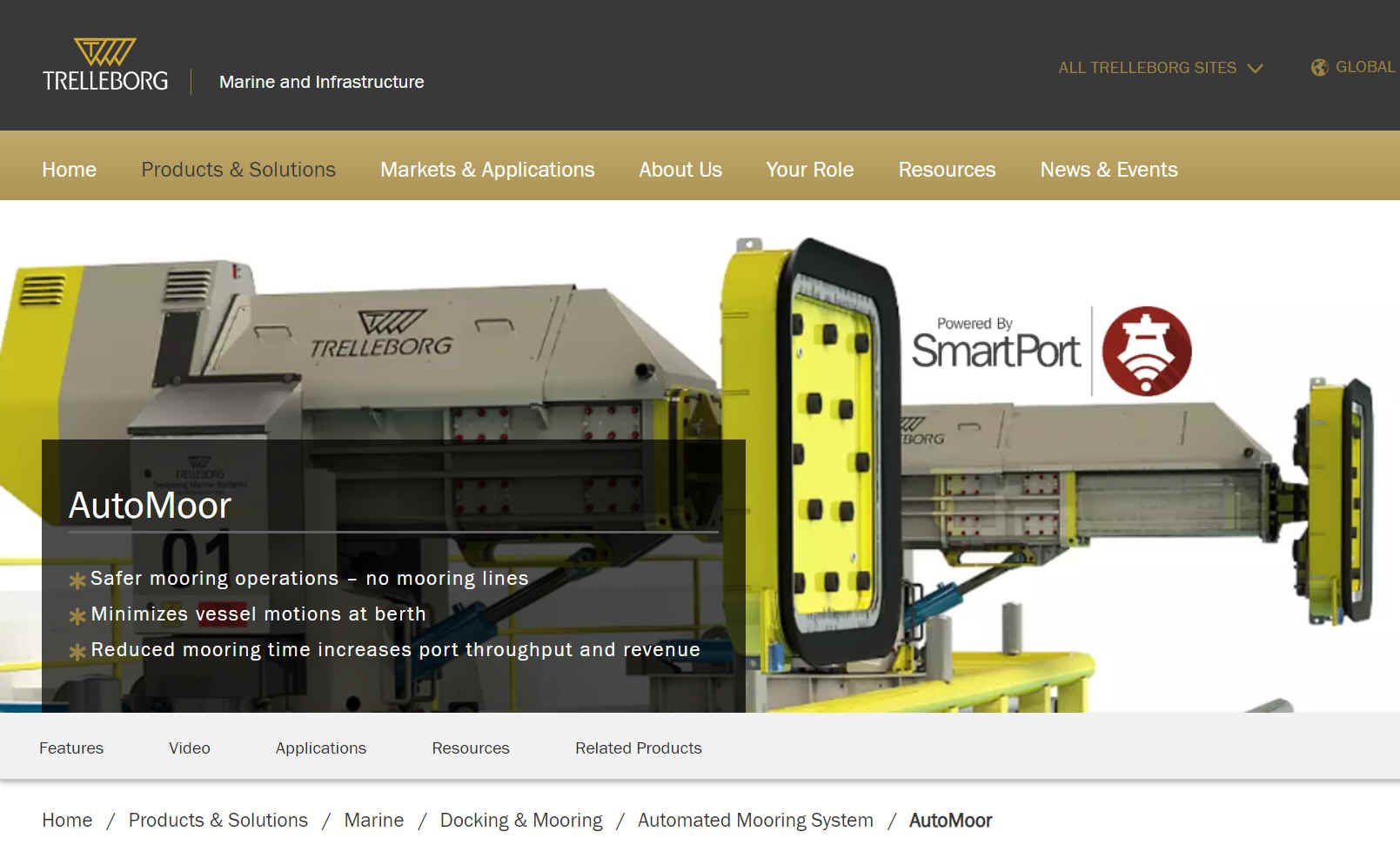
MORE
CAPACITY - AutoMoor is Trelleborg's rope-free, automated mooring system designed to make
berthing operations smarter, safer and more competitive.
AutoMoor units eliminate mooring lines and are specifically designed to improve operational efficiency and enhance safety levels. Combining
vacuum pad and passive damping technology to rapidly attach to and secure a vessel at berth, the units are suitable for a range of environmental and berthing conditions.
AutoMoor uses SmartPort technology to connect assets and to continuously monitor all mooring loads acting on the vessel
while berthed. The system also provides live data to the operator to optimize day-to-day port and terminal operations.
TRELLEBORG
AUTOMATED DOCKING & SMARTER PORTS
Trelleborg’s latest innovation in automated mooring systems optimizes berth utilization and
claims superior efficiencies in port operations. Automated mooring expands the product transfer operational window throughout a greater range of berthing and environmental conditions, improves safety, lowers resource and space requirements, demands less time to moor vessels and can minimize infrastructure investment to increase berthing capacity.
SMARTPORT
SmartPort by Trelleborg powers the critical interface between ship and port, on land and at sea. Building on Trelleborg's history of engineering ingenuity and sector knowledge, with a keen eye on data capture and management, and technology-driven insight, SmartPort technologies can increase efficiencies, improve safety and improve ROI for ports and vessels alike.
AUTOMOOR FEATURES
- Reduces turnaround time for vessels to berth and depart, increasing port throughput
- Dampens vessel motions by reducing peak mooring loads due to surge and sway movements. Port operations can continue safely in a greater range of environmental conditions
- Decreased reliance on tug boats for berthing and de-berthing reduces waiting and scheduling delays
- Decreases port emissions thanks to the reduced time taken to moor the vessel, as ship engine idling is diminished and tug vessel time at berth reduced
- Minimizes infrastructure upgrades while increasing berth capacity, by eliminating the need for wharf extensions or mooring dolphin investments for port terminal upgrades
- Reduces the effects of passing ships in narrow waterways and the long period wave motions experienced in some ports and harbors, by damping motions of the affected vessel
- Removes the need for breakwater infrastructure lowering port and terminal investment requirements
- Reduces peak loads resulting in reduced civil requirements
- SmartPort system integration
Trelleborg Marine and Infrastructure has over 40 years’ experience in providing infrastructure, advanced marine fenders, oil and gas transfer, ship performance solutions, docking and mooring, surface buoyancy and service and support.
They
work with specifiers on a project-by-project basis to determine best-fit solutions and supply fully integrated systems to fulfill
the most demanding specifications for single berths, or an entire port,
their in-house design coupled with manufacturing and installation expertise,
provides a virtual turnkey service designed for operational performance and long-term maintenance is
minimization.
Trelleborg Marine has a state-of-the-art engineering and design center in
India. Their entire product range is manufactured in-house.
Trelleborg are a global organization operating in 50 countries, but still provide local support. Their skilled teams of engineers have worked on over 10,000 projects worldwide.
Trelleborg AB, PO Box 153
231 22 Trelleborg,
Sweden
Email: marine_infra@trelleborg.com
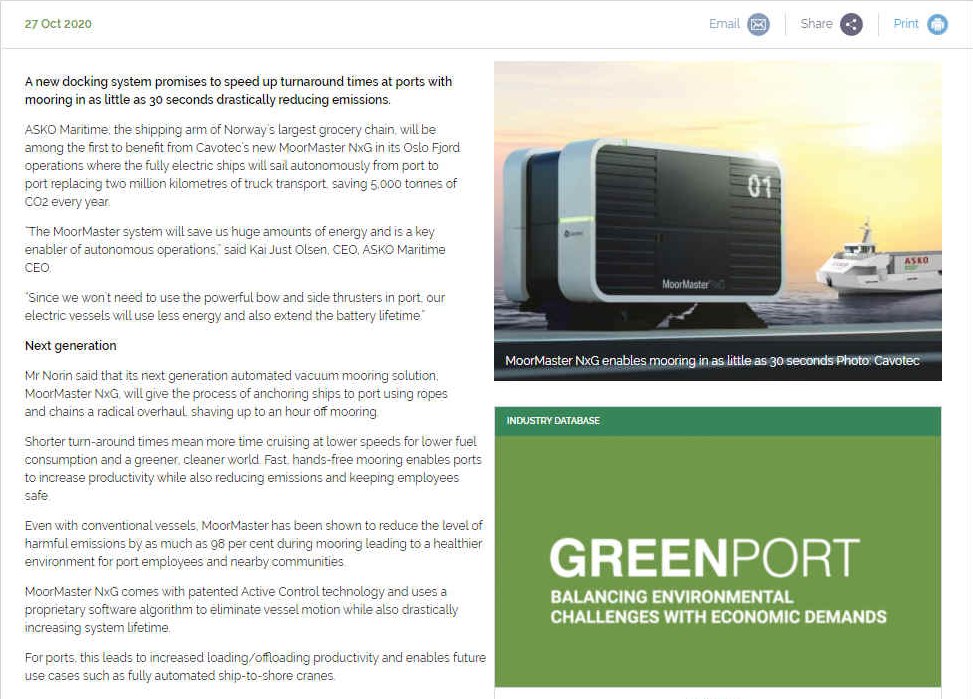
MOORMASTER -
Works with virtually all vessels. The modular design and vacuum pads that attach to any flat surface
Can be used with a wide variety of vessels and applications, irrespective of vessel size and design.
MoorMaster™ systems are used to moor ferries as well as 400m container ships and bulk carriers of more than 300m.
GREENPORT.COM FASTER DOCKING FOR AUTONOMOUS SHIPS 27
OCT 2020
A new docking system promises to speed up turnaround times at ports with mooring in as little as 30 seconds drastically reducing emissions.
ASKO Maritime, the shipping arm of Norway’s largest grocery chain, will be among the first to benefit from Cavotec’s new MoorMaster NxG in its Oslo Fjord operations where the fully electric ships will sail autonomously from port to port replacing two million kilometres of truck transport, saving 5,000 tonnes of CO2 every year.
“The MoorMaster system will save us huge amounts of energy and is a key enabler of autonomous operations,” said Kai Just Olsen, CEO, ASKO Maritime CEO.
“Since we won’t need to use the powerful bow and side thrusters in port, our electric vessels will use less energy and also extend the battery lifetime.”
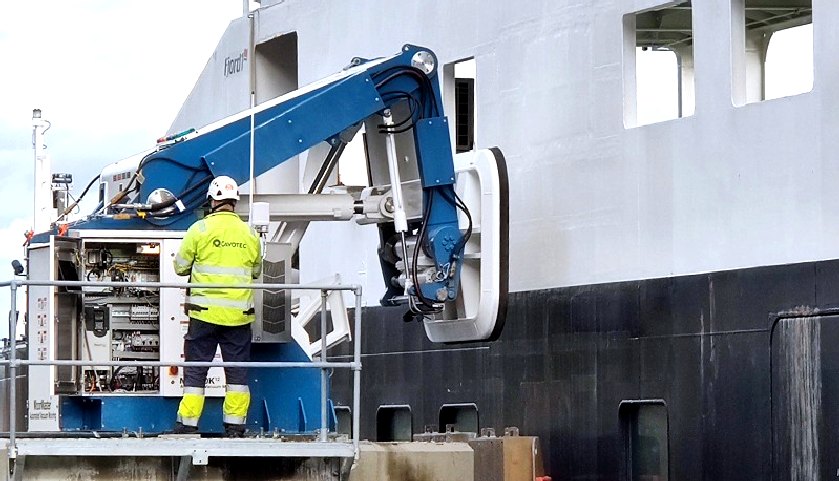
NEXT
GENERATION
Mr Norin said that its next generation automated vacuum mooring solution, MoorMaster NxG, will give the process of anchoring ships to port using ropes and chains a radical overhaul, shaving up to an hour off mooring.
Shorter turn-around times mean more time cruising at lower speeds for lower fuel consumption and a greener, cleaner world. Fast, hands-free mooring enables ports to increase productivity while also reducing emissions and keeping employees safe.
Even with conventional vessels, MoorMaster has been shown to reduce the level of harmful emissions by as much as 98 per cent during mooring leading to a healthier environment for port employees and nearby communities.
MoorMaster NxG comes with patented Active Control technology and uses a proprietary software algorithm to eliminate vessel motion while also drastically increasing system lifetime.
For ports, this leads to increased loading/offloading productivity and enables future use cases such as fully automated ship-to-shore cranes.
Cavotec SA
Via G.B. Pioda 14 - CH-6900 Lugano
Switzerland

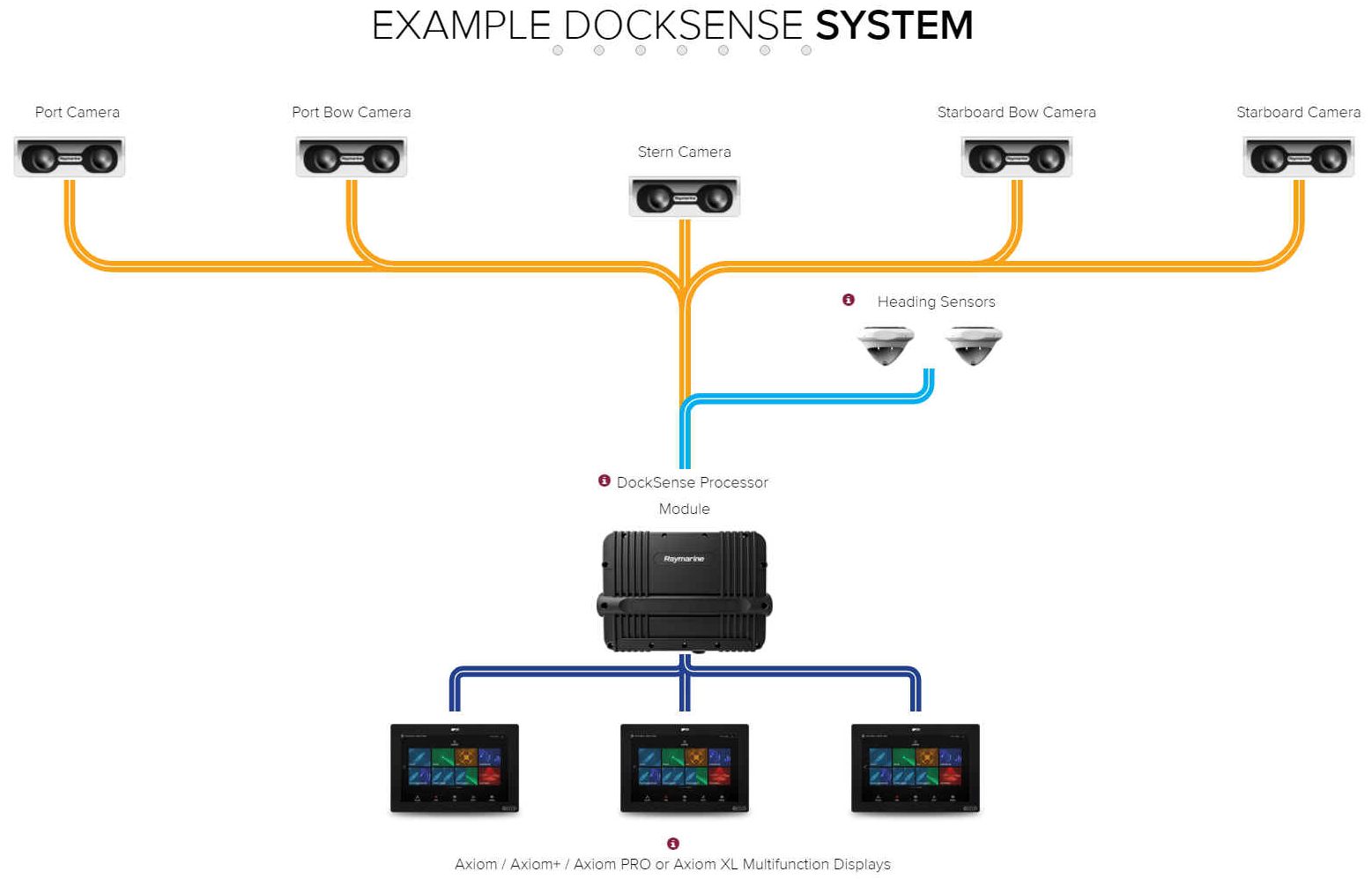
RAYMARINE -
DockSense Alert integrates with Raymarine Axiom® multifunction displays to present a real-time birds-eye view of the vessel and its immediate surroundings. Raymarine's 3D stereo vision cameras deliver live video to the helm and employ advanced motion sensors to measure the distance between the boat and external objects accurately. The system also delivers audible and visual alerts, intelligently informing the captain of any external object's proximity to the vessel. This new level of awareness simplifies docking while mitigating against the effects of wind, tide, and monitoring objects out of sight from the helm.
DockSense Alert systems are designed for professional engineer installation, and each system integrates with Raymarine Axiom multifunction navigation displays. In addition to advanced 3D stereo vision cameras, DockSense Alert systems require precision heading and motionsensing technology in the form of the AR250 and AR270 DockSense heading sensors. The two sensors combine to create a highly accurate GPS compass system, unaffected by magnetic interference. When outfitting a vessel, Raymarine DockSense experts will partner with your engineering team to design a DockSense Alert system that provides maximum coverage and confidence for you.
If you are boat builder or system integrator working with a boat builder, Raymarine DockSense experts can partner with your engineering team to design a DockSense Alert system.
RAYMARINE
- TRANSPORT AUTONOMOUS VEHICLES 23 SEPTEMBER 2019
An
automated docking technology, to take the stress out of boating
A new automated docking system that takes the parking-sensor concept that car drivers are familiar with to the seas
In the same way that technology has helped ease the stress of parallel parking for car drivers, a new automated docking system aims to take the pressure out of mooring a boat.
Sensors stationed around the boat detect obstacles in the water and adjust the engines as the captain moves into dock, making it virtually impossible to collide with another vessel.
The technology could also have applications in the development of autonomous watercraft.
Raymarine — the marine division of US sensor equipment manufacturer FLIR — demonstrated its automated docking system at the 2019 Boat Show in Southampton, UK.
FLIR vice president and general manager of its maritime subdivisions Grégoire Outters said: “When you go out on a boat, the first thing you worry about is leaving the dock and then, while you’re out on the waves, there’s the additional fear of returning to dock.
“When the weather is starting to turn, it can be a stressful experience taking the boat into a slip.
“So this technology was designed to make the task easier and remove any stress.”
How does Raymarine’s automated docking system work?
Raymarine’s DockSense uses a series of stereoscopic cameras positioned around the hull of the boat to give a 360-degree view of its surroundings, as well as judge depth and distance from other objects.
The cameras were originally developed by one of FLIR’s sister companies in Canada, with the purpose of monitoring customer numbers in shopping centres and retail outlets.
Outters said: “It’s a completely different application of the technology, but they need to be able to measure distance to be able to detect and count people accurately.
“In our case, because we needed to be able to measure distance precisely to be able to calculate where the dock is and where other objects are in relation to the boat, we decided to use the same tech.”
As the boat moves in to dock, the velocity of the boat and external elements such as the wind and tide are taken into consideration — factors that would normally have to be judged by the captain — and the data is quickly processed to calculate the trajectory of the vessel.
The system is tied to the engines, which are able to automatically compensate for any movement and hold the boat steady as it moves into port.
A 50cm limit is set around the edge of the boat and if anything comes within this proximity the engines are stopped to prevent the boat crashing.
The automated docking system promises to be simple enough to allow even a novice to dock a 46-foot boat, without the risk of damage.
Outters added: “Over time we plan to use more and more sensors to bring more autonomy into navigation, not only docking, but also being able to navigate more safely while out on the water.
“The next step could be alerting our customers whenever they have a risk of hitting an object on the
water and taking the control of the boat whenever the risk is becoming too high.”
Creating an autonomous boat
Despite his assertion that creating an autonomous system could be possible, Outters admits there is little demand for such a craft.
He said: “We don’t actually don’t want to create a fully autonomous system because, unlike cars, when you go out on your boat, you want to enjoy it.
“It’s not just a case of going from point A to point B, you want to really enjoy being on the water.
“All we want to do is remove the stress and the risk — the captain will still have to be at the helm.”
Luxury boating brand Prestige, which is partnering with FLIR on the project, will have the first boats to be sold with the automated docking system.
Erik Stromberg, director of product marketing for the company, said: “We’re at least 10 or 15 years behind the automotive industry in terms of automation.
“It’s not to say that the system could not be autonomous sometime in the future but, even from a market perspective, there’s very little demand for them.
“Whereas increasing situational awareness, making it more comfortable for the driver and taking the stress out has a more immediate application.”
By Sam Forsdick
Raymarine UK Limited
Marine House
Cartwright Drive,
Fareham, PO15 5RJ
Tel: +44 (0)1329 246 700
Fax: +44 (0)1329 246 701
Email: info@raymarine.com
Service Repair: +44 (0)1329 246 932
Email: emea.service@raymarine.com
Technical Support UK: +44 (0)1329 246 777
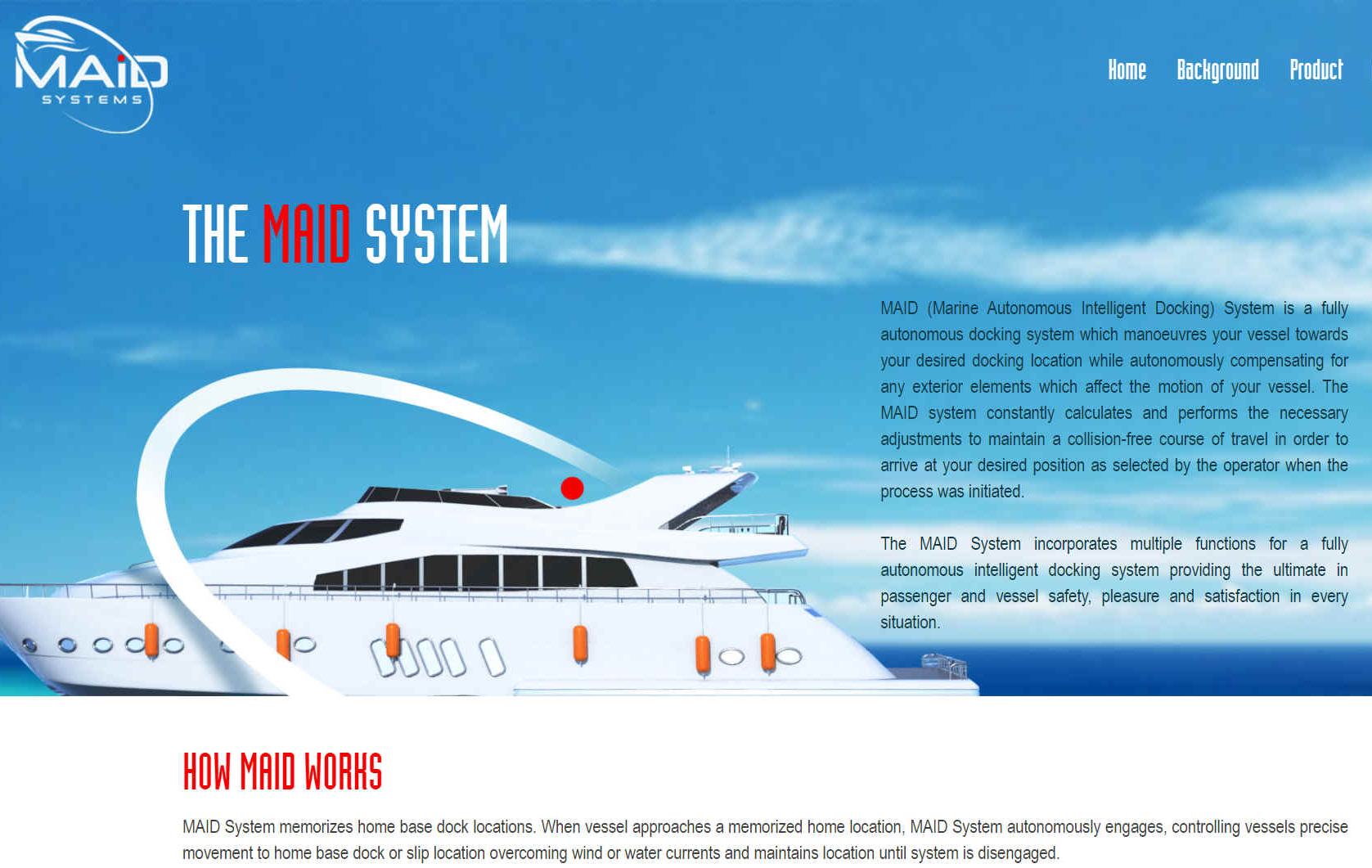
MADE
IN HEAVEN - The Marine Autonomous Intelligent Docking (MAID) system incorporates Photographic and Infrared sensor technologies integrated within the marine vessel to provide surrounding environmental awareness for several hundred feet in real time, allowing the operator to select a target location on the MAID interactive monitor to re-position the vessel autonomously from the present location to a desired position alongside a dock or object.
Using advanced perception technologies, the MAID System recognizes both the vessel’s current position and the selected docking location, and the trajectory of the vessels path is determined and planned by the MAID System. The MAID System validates and pre-determines the target location area is of sufficient area to accommodate the dimensions of the vessel upon which the MAID System engages the drive systems to autonomously maneuver the vessel on the planned collision-free path of travel at a controlled velocity to the selected target location. Using advanced perception technologies, the MAID System recognizes both the vessel’s current position and the selected docking location, and the trajectory of the vessels path is determined and planned by the MAID System.
The MAID System validates and pre-determines the target location area is of sufficient area to accommodate the dimensions of the vessel upon which the MAID System engages the drive systems to autonomously maneuver the vessel on the planned collision-free path of travel at a controlled velocity to the selected target location. The MAID System incorporates dynamic obstacles handling to recognize and track other vessels and objects in the harbor, autonomously rerouting the path as required to maintain a collision free path of travel during the docking procedure. Incorporating A.I. learn-in technology, MAID system collects vessel performance and experiences as MAID operates, building its own knowledge base to become more precise with every operation which makes the MAID System highly adaptable to varying motor vessels. The MAID System autonomously stops the vessel at the target location and maintains the position until the system is disengaged.
FIVE BUSIEST PORTS WORLDWIDE
BY NUMBERS OF CONTAINERS:
1. Hong Kong
2. Singapore
3. Pusan
4. Kaohsiung
5. Rotterdam
BY VOLUME:
1. Rotterdam
2. Singapore
3. South Louisiana
4. Hong Kong
5. Shanghai
LINKS
& REFERENCE
https://www.trelleborg.com/en/marine-and-infrastructure/products--solutions--and--services/marine/docking--and--mooring/automated--mooring--systems
https://unctad.org/news/container-ports-fastest-busiest-and-best-connected
http://www.ecoports.com/
https://www.greenport.com/news101/energy-and-technology/intuitive-docking-for-autonomous-electric-ships
https://alphaliner.axsmarine.com/PublicTop100/index.php
https://www.ns-businesshub.com/transport/automated-docking/
http://maidsystems.com/product/
https://www.bluebird-electric.net/Bluebird_Boats_Ships_Systems/ports_autonomous_approaches_unmanned_boats_navigation.htm
