BUNKERING OF HYDROGEN
FOR SPACE
EXPLORATION The
liquid hydrogen story is long and tortuous in its gestation. In 1874,
Jules Verne predicted that water would be the source of abundant energy,
burning more brightly than coal, the then wonder fuel. But it was to be
a steady stream of advances until the US military wanted to use it is
jet aircraft engines. Then the development dollars began to roll.
Once in the tanks and with the launch countdown nearing zero,
LH2 and LOX are pumped into the combustion chamber of a rocket engine. When the propellant is ignited, the hydrogen reacts explosively with oxygen to
form water:
2H2 + O2 = 2H2O + Energy
This “green” reaction releases massive amounts of energy along with superheated water (steam). The hydrogen-oxygen reaction generates tremendous heat, causing the water vapor to expand and exit the engine nozzles at speeds of 10,000 miles per hour! All that fast-moving steam creates the thrust that propels the rocket from Earth.
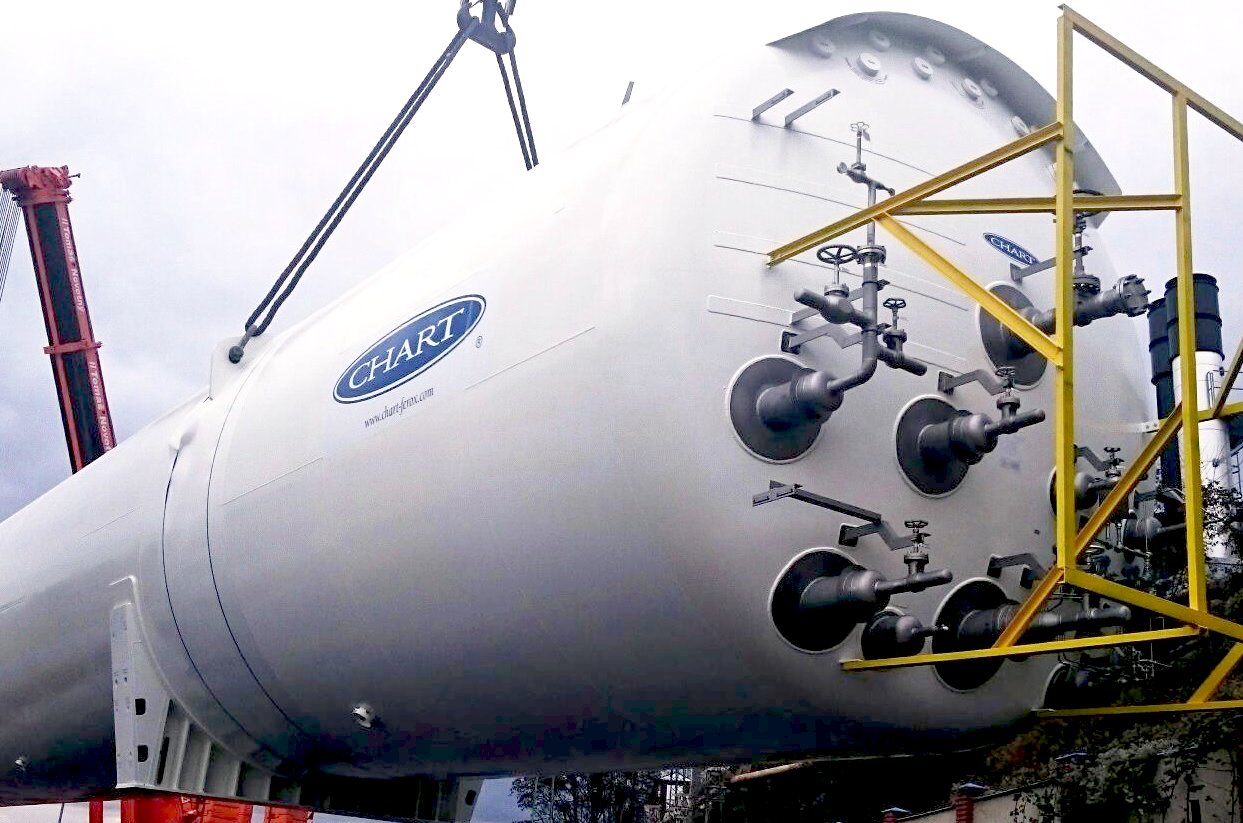
CHART
COMMERCIAL STORAGE TANKS - Liquefied hydrogen has a temperature of -253 °C and is one of the coldest cryogenic gases there is, which places system components and materials under extreme stresses.
Once liquefied, hydrogen is reduced to 1/800th of its volume compared to that of its gas phase, facilitating a more-efficient distribution.
But it needs fuel tanks four times the size of those for petrol. In
Europe, the FCH-JU,
is working hard to promote green hydrogen regeneration from renewable
energy, via industrial scale electrolyzers. This is mainly for cars and
trucks, but hydrogen could be a fuel for ships, provided that the
infrastructure is developed.
Despite criticism and early technical failures, the taming of liquid hydrogen proved to be one of NASA's most significant technical accomplishments.
Hydrogen - a light and extremely powerful rocket propellant - has the lowest molecular weight of any known substance and burns with extreme intensity (5,500°F). In combination with an oxidizer such as liquid oxygen, liquid hydrogen yields the highest specific impulse, or efficiency in relation to the amount of propellant consumed, of any known rocket propellant.
Because liquid oxygen and liquid hydrogen are both cryogenic -- gases that can be liquefied only at extremely low temperatures -- they pose enormous technical challenges. Liquid hydrogen must be stored at minus 423°F and handled with extreme care. To keep it from evaporating or boiling off, rockets fuelled with liquid hydrogen must be carefully insulated from all sources of heat, such as rocket engine exhaust and air friction during flight through the atmosphere. Once the vehicle reaches space, it must be protected from the radiant heat of the Sun. When liquid hydrogen absorbs heat, it expands rapidly; thus, venting is necessary to prevent the tank from exploding. Metals exposed to the extreme cold of liquid hydrogen become brittle. Moreover, liquid hydrogen can leak through minute pores in welded seams. Solving all these problems required an enormous amount of technical expertise in rocket and aircraft fuels cultivated over a decade by researchers at the National Advisory Committee for Aeronautics (NACA) Lewis Flight Propulsion Laboratory in Cleveland.
Today, liquid hydrogen is the signature fuel of the American space program and is used by other countries in the business of launching satellites. In addition to the Atlas, Boeing's Delta III and Delta IV now have liquid-oxygen/liquid-hydrogen upper stages. This propellant combination is also burned in the main engine of the Space Shuttle. One of the significant challenges for the European Space Agency was to develop a liquid-hydrogen stage for the Ariane rocket in the 1970s. The Soviet Union did not even test a liquid-hydrogen upper stage until the mid-1980s. The Russians are now designing their Angara launch vehicle family with liquid-hydrogen upper stages. Lack of Soviet liquid-hydrogen technology proved a serious handicap in the race of the two superpowers to the Moon.4 Taming liquid hydrogen is one of the significant technical achievements of twentieth century American rocketry.
ABOUT HYDROGEN
Hydrogen is the simplest element, a molecule of two atoms, a gas at normal conditions, colorless, odorless, nontoxic but asphyxiating, and non-corrosive but reactive. It occurs In many substances, the most common of which is water, and ranks ninth in abundance of the chemical elements on the earth. Active chemically, hydrogen exists free only in minute quantities. There is plenty of hydrogen in stars, and Jupiter is believed to be made up entirely of hydrogen in several forms under intense pressure.
Only helium is more difficult to liquefy than hydrogen. At atmospheric pressure, hydrogen boils at 20.3 K. It is the lightest element; its liquid density is 1/14 that of water.
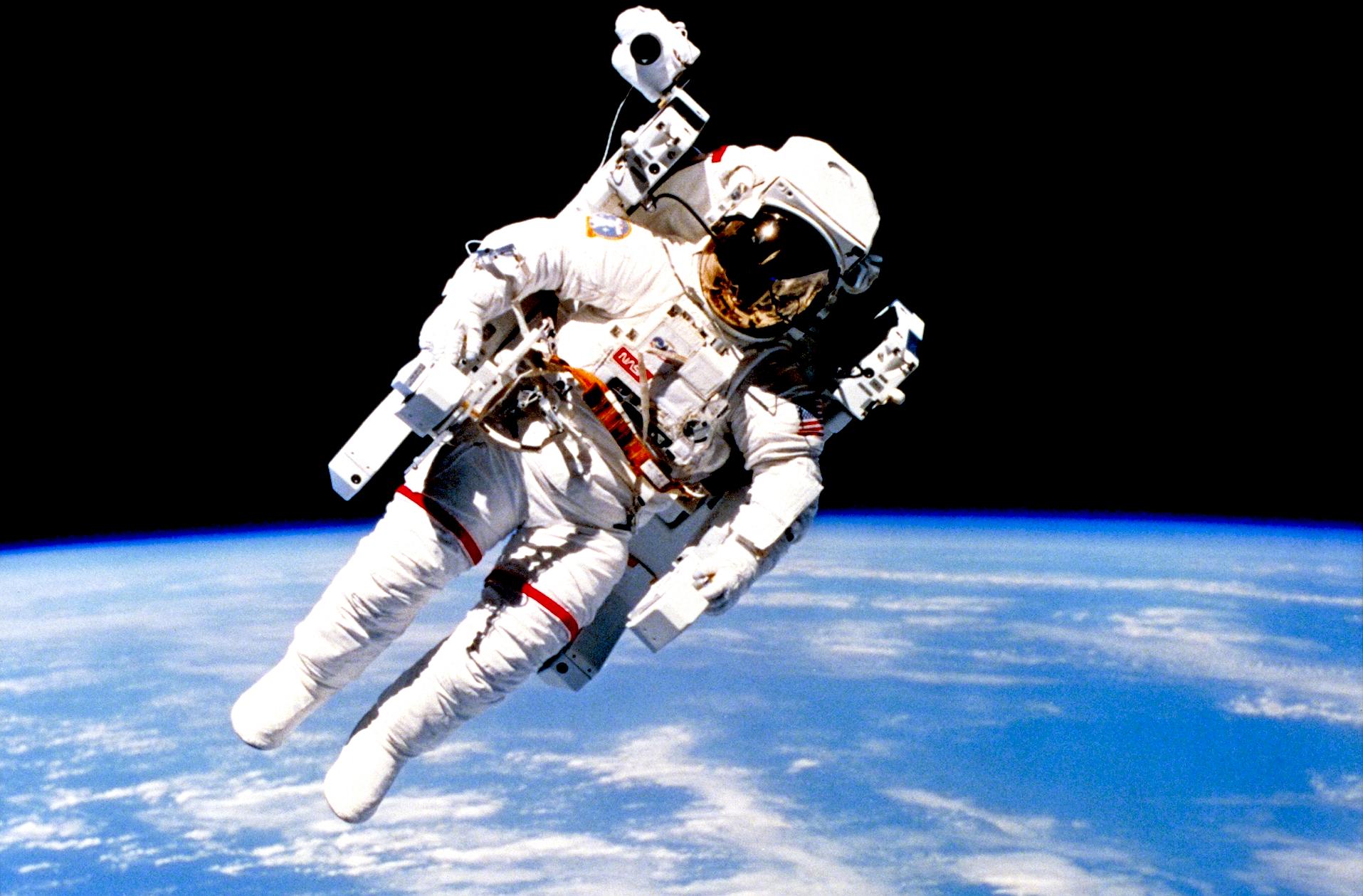
SUNTAN
- TOP SECRET MILITARY PROJECT
The largest and most extraordinary project for using hydrogen as a fuel was carried out by the Air Force in 1956-1958 in
super-secrecy. Very few people are aware of it, even now, yet over a hundred million dollars were spent-perhaps as much as a quarter of a billion dollars. Although the project was cancelled before completion, it led directly to the first rocket engine that flew using hydrogen. The project was code-named Suntan, and even this was kept secret.
The Army's principal missile team was formed around 120 German rocket experts brought to the United States in 1945.
By the end of 1955, the US Air Force had in progress a number of research and development activities on the feasibility of using liquid hydrogen in flight. The Garrett Corporation, which bought Rae's patents and formed a Rex division with Rae as chief engineer, was three months into a contract for design studies of Rex engines and had concentrated on the largest and latest, the air-breathing Rex III. Kelly Johnson's Skunk Works at Lockheed Aircraft, past their peak effort in designing and building prototype U-2s for the CIA, was two months into a three-month design study of hydrogen-fueled aircraft for Garrett. United Aircraft (now United Technologies) was in the second quarter of a study of using hydrogen in a conventional turbojet engine, and a competitor, General Electric, was also showing interest in hydrogen. Beech Aircraft and Garrett were investigating liquid hydrogen tanks, insulation, and behavior of hydrogen in storage. The Air Force and NACA agreed that the Lewis laboratory would determine the feasibility of flying an airplane fueled with liquid hydrogen. The Air Force would provide the estimated $1 million needed, as well as lend equipment.
Kelly Johnson saw his task as much more than designing and building a
hydrogen fueled airplane. He was also concerned about its operation, for if it was to be successful, liquid hydrogen had to be produced and shipped in quantity and be handled like gasoline. On 16 March 1956, he and his staff met with representatives of J.H. Pomeroy and Company of Los Angeles, a consulting engineering firm. Johnson wanted Pomeroy to study the engineering feasibility and cost of producing
para-hydrogen in quantity, and he was interested in three production rates-45 000, 135 000, and 225 000 kilograms per day. He wanted the plant location to be in the Antelope Valley of California. Pomeroy agreed to undertake the study, and ten days later Johnson sent them a letter of intent with ground rules.12
At the outset of the project, Johnson assigned one of his assistants, Ben Rich, a thermodynamics and heat transfer expert, the dual responsibilities of propulsion and the handling of hydrogen. Rich, who knew little about liquid hydrogen at the time, checked Mark's Mechanical Engineering Handbook which stated that liquid hydrogen was an impractical fluid and only a laboratory curiosity. He was to understand why in his subsequent visits to laboratories and firms working with liquid hydrogen. Among those contacted were Professor William Giauque, University of California at Berkeley, and Russell B. Scott at the Cryogenic Laboratory of the U.S. Bureau of Standards at Boulder. Rich concluded that liquid hydrogen was mostly in the hands of highly skilled scientists, and few of them appreciated the practical problems he saw in adapting liquid hydrogen to routine use as an airplane fuel. In that application, a temperature range from the boiling point of liquid hydrogen, 20.3 K, to the frictional temperature of the airplane skin at Mach 2.5, about 670 K, had to be handled with designs and materials dictated by volume and weight restrictions. The earthbound design and construction methods used with liquid hydrogen generally were unsuitable. Moreover, Rich found that he was thinking of far greater quantities of liquid hydrogen than others; he used the unit "acre-feet" to emphasize his point.
All these considerations made it obvious that the Skunk Works staff had to learn how to handle liquid hydrogen and to adapt it to the particular application.
This required a liquid hydrogen test facility. During World War II, a bomb shelter revetment had been built adjacent to the Skunk Works, and it was selected as the site of the hydrogen facility. It was named "Fort Robertson" after the man who was in charge of the test operations. A Collins cryostat, capable of producing nine liters of liquid hydrogen per hour, was installed to test materials, bearings, seals, and small components. When larger quantities were needed for tank flow and spill tests, liquid hydrogen was obtained from the Bureau of Standards Cryogenic Laboratory at Boulder and stored in a 2200 liter refrigerated dewar built by the Air Force for the hydrogen bomb program. The Skunk Works also relied heavily on the experts at the NBS Cryogenic Laboratory, particularly Russell Scott, regarded as "Mr. Hydrogen," who became a consultant.
On 1 October 1956, the J.H. Pomeroy Company reported on hydrogen liquefaction plants. The report is an excellent summary of the state-of-the-art, and cites 52
references. An entire plant was planned-from incoming natural gas for producing gaseous hydrogen to underground storage of liquid hydrogen. A plant of 45 000 kilograms per day capacity was studied in detail, as well as multiples of it-well above
the size of the Boulder installation, which had the largest capacity in existence in the U.S. Pomeroy considered the 45 000 kilogram per day capacity to be about the largest practical size. Construction cost was estimated at $45 million and operating costs at $0.386 per kilogram. A million cubic meters of natural gas per day would be required.* Pomeroy discussed an expansion engine process that would. with some additional R&D, be available. With catalysts, it would permit continuous liquefaction of parahydrogen.
For a hydrogen-fueled airplane, the very low temperature and density of liquid hydrogen pose special design problems for tanks, pumps, lines, instrumentation, and other components in the fuel system. The special requirements imposed by hydrogen are recognized immediately by all who consider such designs and, of course, received major attention by the men of the Skunk Works. The CL-400 design divided the hydrogen tankage into three sections; the forward tank had a capacity of 67 000 liters; aft, 54 000; and center (sump), 15 000. The two main tanks were kept at 2.3 atmospheres pressure and the sump tank slightly lower for fuel transfer. In the sump was a booster pump, built by Pesco Products, that supplied liquid hydrogen to the engines at a pressure of 4.4 atmospheres. The engines were mounted at the wing tips, which meant that the liquid hydrogen had to pass through a hot wing with surface temperatures up to 436 K. The design provided a vacuum-jacketed, insulated line for this purpose.
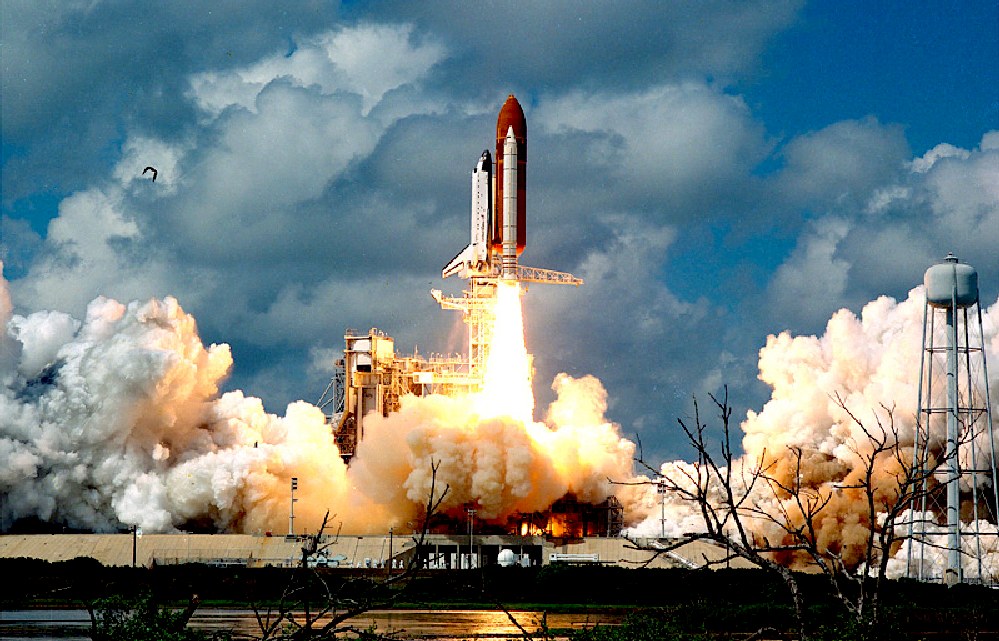
To
save launch weight, the cryogenic external Super Light Weight Tank (SLWT)
was not painted
There were many unknowns in the design of the hydrogen tanks and other fuel components, and numerous experiments were conducted to obtain more information. These were done at Fort Robertson and included half-scale models of the sump tank, the vacuum-jacketed lines for carrying hydrogen from the tanks through the hot wings to the engines, booster pumps, valves, controls, and other components. These were tested in thermal environments simulating flight conditions. Later a full-scale sump pump was built and shipped to Pratt & Whitney for their use in engine testing.
Among the first concerns of Johnson and Rich were the fire and explosion hazards of hydrogen. Could it be handled as safely as gasoline? In his early visits to laboratories using liquid hydrogen, Rich inquired about fires and explosions, but obtained little information. The laboratories went to great lengths to avoid these problems. The only previous explosions Rich learned about were some minor ones Professor William Giauque experienced when oxygen crystals formed in a heat exchanger containing hydrogen. The paucity of information led Johnson and Rich to devise a series of experiments to determine for themselves the hazards of hydrogen fires and explosions.
For this they turned to their only testing ground, Fort Robertson-less than a kilometer from the runways of the Burbank airport.
Tests were devised in which tanks containing liquid hydrogen under pressure were ruptured. In many cases, the hydrogen quickly escaped without ignition. The experimenters then provided a rocket squib (a small powder charge) to ignite the escaping, hydrogen. The resulting fireball quickly dissipated because of the rapid flame speed of hydrogen and its low density. Containers of hydrogen and gasoline were placed side by side and ruptured. When the hydrogen can was ruptured and ignited, the flame quickly dissipated -, but when the same thing was done with gasoline, the gasoline and flame stayed near the container and did much more damage. The gasoline fire was an order of magnitude more severe than the hydrogen fire. The experimenters tried to induce hydrogen to explode, with limited success. In 61 attempts, only two explosions occurred and in both, they had to mix oxygen with the hydrogen. Their largest explosion was produced by mixing a half liter of liquid oxygen with a similar volume of liquid hydrogen. Johnson and Rich were convinced that, with proper care, liquid hydrogen could be handled quite safely and was a practical fuel-a conclusion that was amply verified by the space program in the 1960s. At the time, however, Johnson and Rich filmed their fire and explosion experiments to convince doubters.
The confidence of Johnson and Rich in hydrogen handling was not always shared by their hydrogen consultant, Russell Scott, who was often amazed at what he saw going on in the test areas of Fort Robertson.14 The facility, however, was well equipped with an explosion-proof electrical system, non-sparking safety tools, hydrogen sniffers or monitors, and other safety devices. In the three years of work and the handling of thousands of liters of liquid hydrogen, there was not a single accident caused by hydrogen. There was, however, one close call. In keeping with Kelly Johnson's philosophy of austerity, the ovens used for simulating hot wing temperatures of Mach 2.5 flight were made partially of wood. There were five such ovens, and early one morning, about 2 a.m., one of them caught fire. The Skunk Works personnel, including Rich, were summoned because the fire department could not be called, for security reasons. At the time there were 2000 liters of liquid hydrogen stored in the area and Rich decided that the best course of action was to dump the liquid hydrogen on the ground. It was winter and very humid; the cold hydrogen quickly filled the revetment with fog about five feet thick. Rich and about two dozen other people were in the revetment and all they could see of each other were their heads, an eerie sight. Luckily, the hydrogen did not ignite.
Cryogenic Laboratory at Boulder. Inspection of the liquefaction plant convinced him that production of liquid hydrogen would be a major obstacle to military use of hydrogen. The plant was small and the laboratory techniques required highly skilled personnel.
By the fall of 1957, J-57 engine experiments demonstrated beyond question that a conventional turbojet could be readily adapted to use hydrogen. Such engines could have been used to meet Kelly Johnson's tight airplane development schedule, but modifying an existing turbojet could not optimize the advantages of hydrogen. The Pratt & Whitney engineers had realized this early in their studies, as had their counterparts in the Rex division of Garrett and the Air Force.
By mid-August 1956, Pratt & Whitney engineers had designed the new engine to use hydrogen. It was designated the "304," taken from the division's engine order number 703040, 16 April 1956.
During the testing period, Coar and Mulready designed and built a second model of the 304 engine, which had an additional (fifth) compressor stage and lower specific fuel consumption. The first 304-2 was assembled at East Hartford on 20 June 1958 and four days later was operated at the Florida test center. Tests continued for a month, with 3 1/3 hours of accumulated running time with hydrogen before the engine experienced a complete turbine failure. It was removed for repair and strengthening of the turbine disks. While this engine was in the shop, another 304 engine (presumably of the first design) was installed and operations began in mid-August. This engine operated satisfactorily through September and accumulated over 6 hours time using hydrogen.
Neither was destined to run again, for time had run out on the Suntan project. In all, the engines were operated 25 1/2 hours with hydrogen, and all indications were that the development was proceeding satisfactorily.
In his survey of industrial firms, Brill found that there was plenty of gaseous hydrogen capacity by several processes. One firm produced excess hydrogen as a byproduct in Painesville, Ohio. This was near Pesco Products division of Borg Warner Corporation, a firm Appold had involved in developing a liquid hydrogen transfer pump for the CL-400 airplane. It was also near the NACA Lewis Laboratory, which would soon need liquid hydrogen for its flight investigation. For these reasons, the Air Force contracted with Air Products, about May 1956, to build a 680-kilogram-per-day liquid hydrogen plant in Painesville. At the same time, two other contracts for similar size plants were awarded. One was to Stearns-Roger for a plant at Bakersfield, California, to support the CL-400 program at Lockheed and the other was to HydroCarbon Research for a plant to support Pratt & Whitney at East Hartford. The Painesville plant was named "Baby Bear" and was the first to become operational, in May 1957, at a cost of $2 million. The California plant was placed into operation in the fall of 1957, but the contract with Hydro-Carbon Research was cancelled for budgetary
reasons. Pratt & Whitney's initial hydrogen needs at East Hartford, over its own capacity, were supplied by truck from Baby Bear.
Another of Brill's tasks was the transportation of liquid hydrogen. Specifications for over-the-highway trailers had been drawn up by Wright Field and a contract was awarded to the Cambridge Corporation. Concurrently, permission was sought and obtained from the Interstate Commerce Commission to transport liquid hydrogen over the highway. The trailers were labeled "flammable liquid," since to reveal the true contents would blow the security cover. The U 1 semi-trailer built by the Cambridge Corporation had a capacity of 26 500 liters, with a hydrogen loss rate of approximately 2 percent per day. Figure 46 shows the U-1 and its successor, the U-2. The latter's specifications were issued on 15 March 1957 because the U-1 ran into a natural, but unanticipated, problem. The very low density of hydrogen made tandem axles on the semi-trailer unnecessary, so the U-1 had only one. During subsequent use of this equipment, there occurred an endless series of problems, all stemming from the single axle, which was unheard of for such a large trailer. It seems that each time one of these large semi-trailers went through a state weighing station, it roused suspicion, doubt about the equipment, and inquiries about the nature of the load.* The Suntan team considered painting a false second axle on the trailer but this was too obvious, and they gave in by ordering the U-2 with its second axle-one that was not needed for the load but which raised no questions on the
road.
To satisfy the anticipated demands for liquid hydrogen at Pratt & Whitney's Florida test center, the Air Force decided to locate a large hydrogen liquefaction plant nearby. United Aircraft obligingly deeded a tract of land to the government for the plant. The Air Force was unsuccessful in interesting private capital to put up the plant, so it funded its construction and operation by Air Products. The plant, with a 4500 kilogram-per-day capacity, was placed in operation in the fall of 1957, at a cost of $6.2 million.
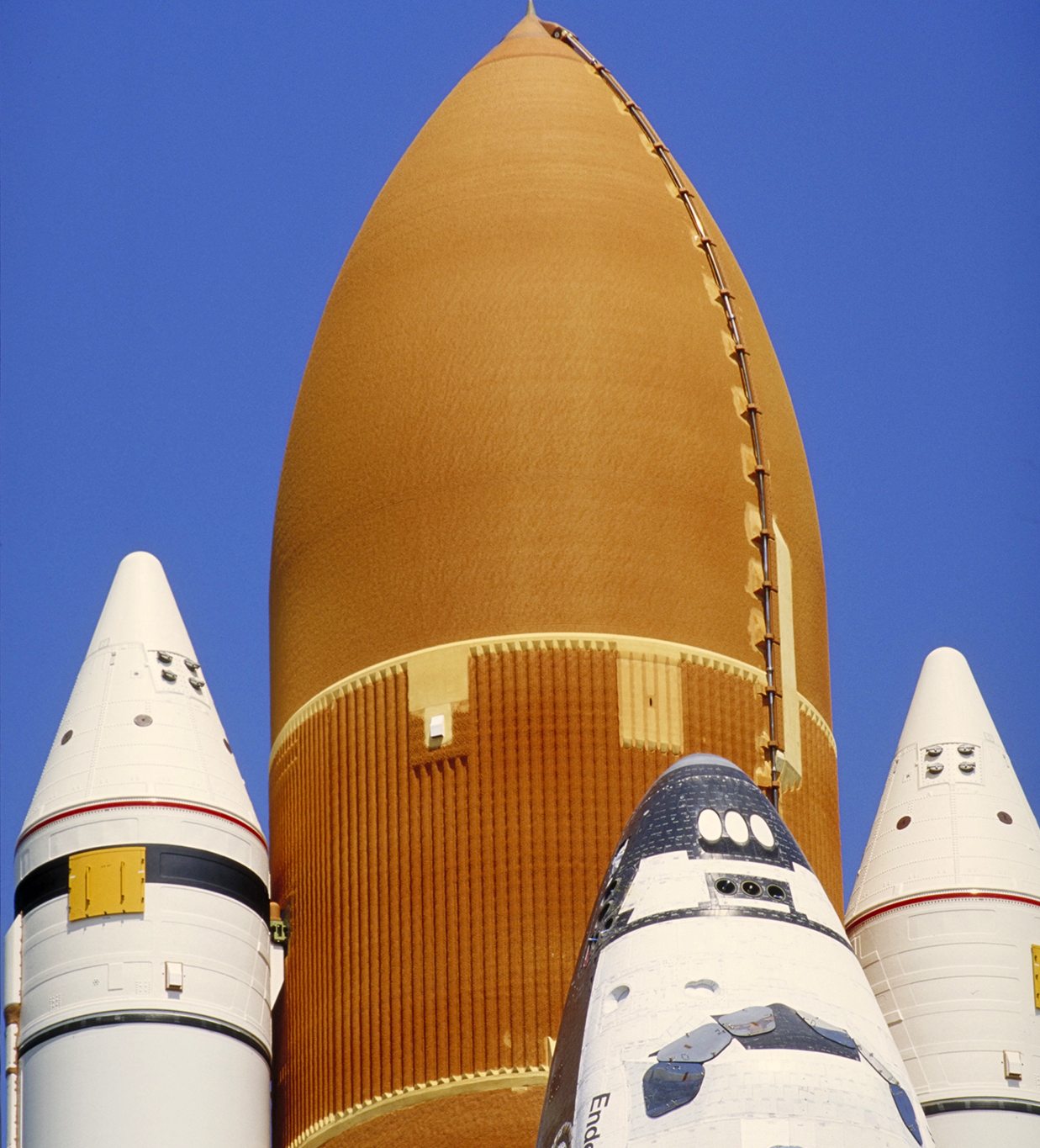
MAMA
BEAR
The Suntan team called this plant "Mama Bear," but locally it was known as the APIX fertilizer plant. APIX was an acronym for Air Products Incorporated, Experimental; the fertilizer association was encouraged by the Air Force and Air Products to conceal the true identity of the product.** Mama Bear used crude oil 'in a chemical process to obtain gaseous hydrogen. Liquid hydrogen storage tanks at the plant were connected to the Pratt & Whitney test cells by a double-wall,
vacuum-jacketed 7.5-centimeter line, 610 meters long. By April 1958, the line had carried 833 000 liters of liquid hydrogen at rates up to 1700 liters per minute for component and engine tests.
Even before Mama Bear was completed, the Air Force planned a much larger hydrogen liquefaction plant to meet the anticipated testing needs of the 304 engine development. The contract was awarded to Air Products in 1957, and the plant was built a few hundred yards away from Mama Bear. It cost $27 million and when placed into operation in January 1959, had a capacity of 27 200 kilograms per day-the world's largest. Crude oil was first used to obtain gaseous hydrogen but later methane was used. This plant, called "Papa Bear," came too late for the Suntan program but served a very useful role in the space program that followed.
What was learned with the Suntan project? The technology of liquid hydrogen was advanced in several ways. There is concurrently a revival of interest in hydrogen-fueled aircraft. As before, however, their potential value is controversial. NASA held a special conference on hydrogen-fueled aircraft in 1973 and has sponsored industry design studies of both subsonic and supersonic configurations. Although no specific development has started, NASA continues to sponsor research applicable to hydrogen-fueled aircraft.
The hydrogen airplane did not materialize, but the liquid hydrogen plants and test facilities constructed by the Air Force would find full utilization in the emerging space program.
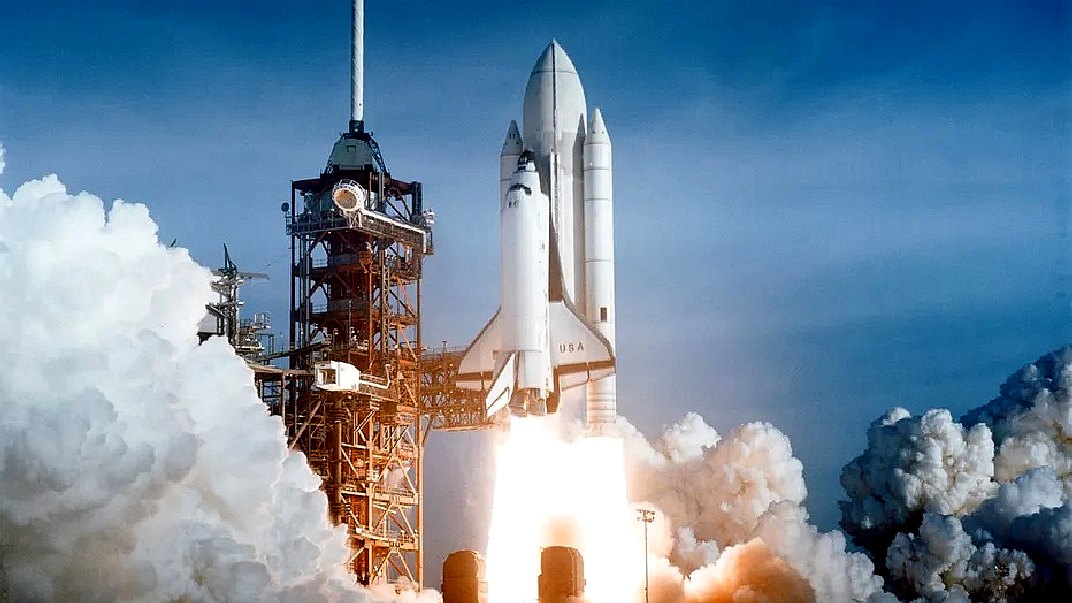
To
begin with and for publicity purposes, the cryogenic tanks were painted.
SPUTNIK
I
The Soviet Sputnik I provided the spur for action in the USA. The news media reflected astonishment, dismay, and fear. American pride was hurt, competitive spirit aroused, and a determination to "catch up" with and exceed the Russians became evident.
In early 1958, when the Soviet Union and the United States had each launched two satellites, it was obvious, from comparing their weights, that the Soviets were using a much more powerful launch vehicle. This led to great concern in the United States about the apparent lag in vehicle capability-a concern welcomed by space enthusiasts for it meant more support.
Sputnik unleashed all the pent-up desires of U.S. space proponents in both the military and civilian sectors.
The coming of Sputnik and U.S. plans for a strong space program quickly produced action, the first high-energy upper stage authorized for development used liquid hydrogen-oxygen. The decision, and subsequent development, owed much to an earlier Suntan program.
In August 1958, the ARDC was authorized to proceed with the development of a hydrogen-oxygen engine.
The first rocket stage to fly using liquid hydrogen and liquid oxygen as propellants was the Centaur stage on top of an Atlas intercontinental ballistic missile.
On 29 July 1958, President Eisenhower signed a bill creating the National Aeronautics and Space Administration; and on the next day, he asked Congress for $125 million for NASA operations. Silverstein's spaceflight budget reflected confidence that NASA would develop large engines and launch vehicles for manned flight and high-energy upper stages for unmanned vehicles.
Competition in large launch vehicles between NASA, ARPA
(Advanced Research Projects Agency), Air Force, and Army, begun in 1958, continued into 1959. The government settled the issue by selecting Saturn as the single large vehicle to serve all needs.
Juno V evolved into Saturn I, and the very large vehicle NASA called Nova evolved into Saturn V, the vehicle used in the Apollo missions of the 1960s and 1970s.
Saturn configurations were restudied as part of the national commitment in 1961 for a manned lunar landing, but one basic concept established by Silverstein did not change: the use of hydrogen in all Saturn upper stages.
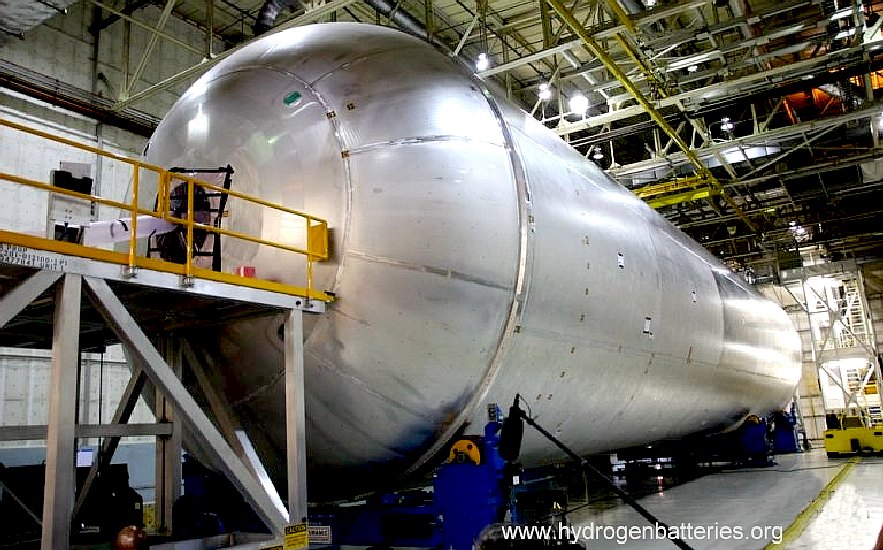
Chemistry is at the heart of making rockets fly. Rocket propulsion follows Newton’s Third Law, which states that for every action there is an equal and opposite reaction. To get a rocket off the launch pad, create a chemical reaction that shoots gas and particles out one end of the rocket and the rocket will go the other way.
But for that to happen, you need to have sufficient energy - and that
means larger tanks for more payload.
LIQUEFACTION
Gas liquefaction techniques up to 1895 involved three basic steps:
1) compressing the gas to a high pressure, usually 50 atmospheres or more,
2) chilling the compressed gas to as low a temperature as possible using various cooling methods, and
3) expanding the chilled, compressed gas slowly from a high to a lower pressure by means of a needle valve.
The cooling methods included, for example, evaporating an ethersolid carbon dioxide mixture or evaporating liquid ethylene, which Wroblewski used in liquefying oxygen. The third step made use of the Joule-Thomson effect for gases, based on experiments by Joule in 1845 and later refined by Thomson. They found that a gas, in slowly expanding from a high to a lower pressure, undergoes a change in temperature.
The gas may be either heated or cooled by the expansion, depending upon the initial temperature and the particular gas. For most gases at room temperature, expansion results in cooling, as anyone who has used an aerosol can or operated a carbon dioxide fire extinguisher has experienced. Compressed air initially at 273 K, for example, will drop about 1/4 K for each atmosphere drop in pressure, while carbon dioxide will drop 11/2 K for each atmosphere drop in pressure. The temperature below which an expansion produces cooling is called the inversion temperature; it is high for most gases, but for hydrogen, it is about 193 K. Hydrogen, therefore, must be cooled below this temperature before it is expanded.
Regenerative cooling means using a fluid as the coolant in a process in which the fluid is itself involved. In the liquefaction of gases, it means that the gas that is cooled by the Joule-Thomson expansion process is later used to cool the incoming compressed gas before expansion.
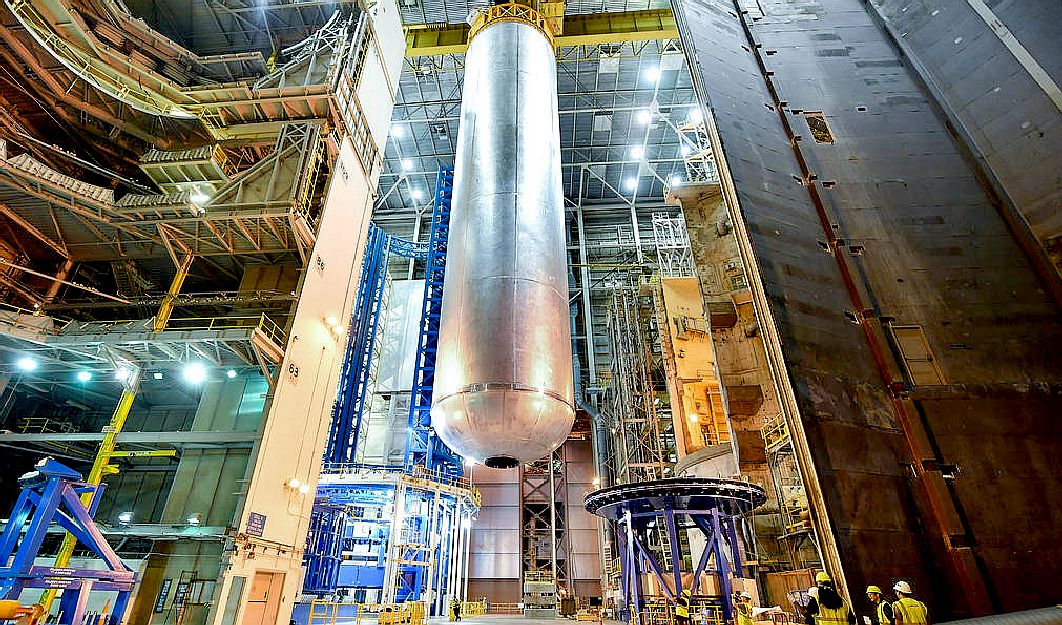
The regenerative cooling concept was an old idea, first introduced by Siemens in 1857 and used by Kirk, Coleman, Solvay, Linde, and others in refrigeration apparatus. In 1895, and within two weeks of each other, William Hampson in England and Carl
von Linde in Germany obtained patents for equipment to liquefy air using tile JouleThomson expansion process and regenerative
cooling. Linde described his apparatus to physicists and chemists at Munich in 1895. A number of publications appealed that same year, among them one by James Dewar, English physicist and chemist who described his apparatus for liquefying air using regenerative cooling.
Hampson's process for liquefying air was simple. He compressed air to 200 atmospheres, expanded it to one atmosphere, and passed the expanded, cooled air through a baffled heat exchanger to cool the incoming compressed air. His method was not very efficient, using power at a rate equivalent to 3.7 kilowatts to produce 1 liter per hour of liquid air. Hampson had his apparatus working at Brin's Oxygen Works by April
1896.
Linde's approach was more complex than Hampson's, but it was also more efficient and suitable for large-scale production of liquid oxygen, nitrogen, and air. He used two stages of gas compression, precooled the air with a separate ammonia refrigeration system, and employed a coiled-tube heat exchanger having three concentric tubes for regenerative cooling. The heat exchanger was insulated by a wood case filled with wool.
Regenerative cooling proved to be the technological link needed to liquefy hydrogen. On 10 May 1898, James Dewar used it to become the first to statically liquefy hydrogen. Using liquid nitrogen he
pre-cooled gaseous hydrogen, under 180 atmospheres, then expanded it through a valve in an insulated vessel, also cooled by liquid nitrogen. The expanding hydrogen produced about 20 cubic centimeters of liquid hydrogen, about 1 percent of the hydrogen
used.
Dewar measured the density of liquid hydrogen at 0.07 kilogram per liter, the modern value, which is 1/14 the density of water and about 1/12 the density of kerosene or gasoline.
The insulated vessel Dewar used was the vacuum container flask he developed earlier which became known as "Dewar flasks," now simply dewars. His design was a very significant contribution to the storage and transportation of very cold liquefied gases such as oxygen, nitrogen, air, hydrogen, fluorine, and helium. Dewars are double-walled vessels with a vacuum in the annular space to minimize heat transfer by conduction and convection. The walls are silvered to reflect radiant heat. Following liquefaction of hydrogen, Dewar became very confident about storing and transporting it in his vacuum vessels, predicting that it could be handled as easily as liquid air. Dewar vessels, with engineering refinements, are used today to transport liquid hydrogen with very low loss rates.
By 1900, then, many of the major properties of gaseous and liquid hydrogen were known. Liquid air, oxygen, and nitrogen were being produced in quantity. Hydrogen had been liquefied, and dewar flasks made its storage and transportation feasible. Suggestions for using liquid hydrogen were not long in coming. The use of gaseous hydrogen for ballooning and its loss from venting brought a suggestion for using liquid hydrogen by storing and evaporating it In a double-walled bag. Of greatest interest to our story, however, was a suggestion made by an obscure Russian schoolteacher, barely five years after Dewar's accomplishment, to use liquid hydrogen to fuel a space rocket.
Carl von Linde's air liquefaction equipment, capable of liquefying 8 liters per hour, was exhibited in Paris in 1900 and purchased by the College of France.7 In 1902, a process for separating oxygen from air, developed by Georges Claude, was in commercial operation in France. Two years later the British Oxygen Company exhibited a hydrogen liquefier, designed by James Dewar, at the Louisiana Purchase Exhibition in St. Louis. The National Bureau of Standards purchased it for $2400 for low-temperature
thermometry. By 1905, Linde liquefaction plants were operating in both Germany and France, and in 1907 the Linde Air Products Company began operations in the United States.
E. W. Washburn discovered that hydrogen and deuterium could be separated by electrolysis. When water is electrolyzed and hydrogen gas escapes, the residual water contains a greater proportion of deuterium oxide (heavy water). This discovery led Norway to undertake large-scale production of heavy water at a hydroelectric plant at Rjukan. Since heavy water is a good moderator for atomic reactors, the Allies raided the Norwegian plant during World War II to prevent Germany obtaining a supply of the isotope.
(Film: The Heroes of Telemark)
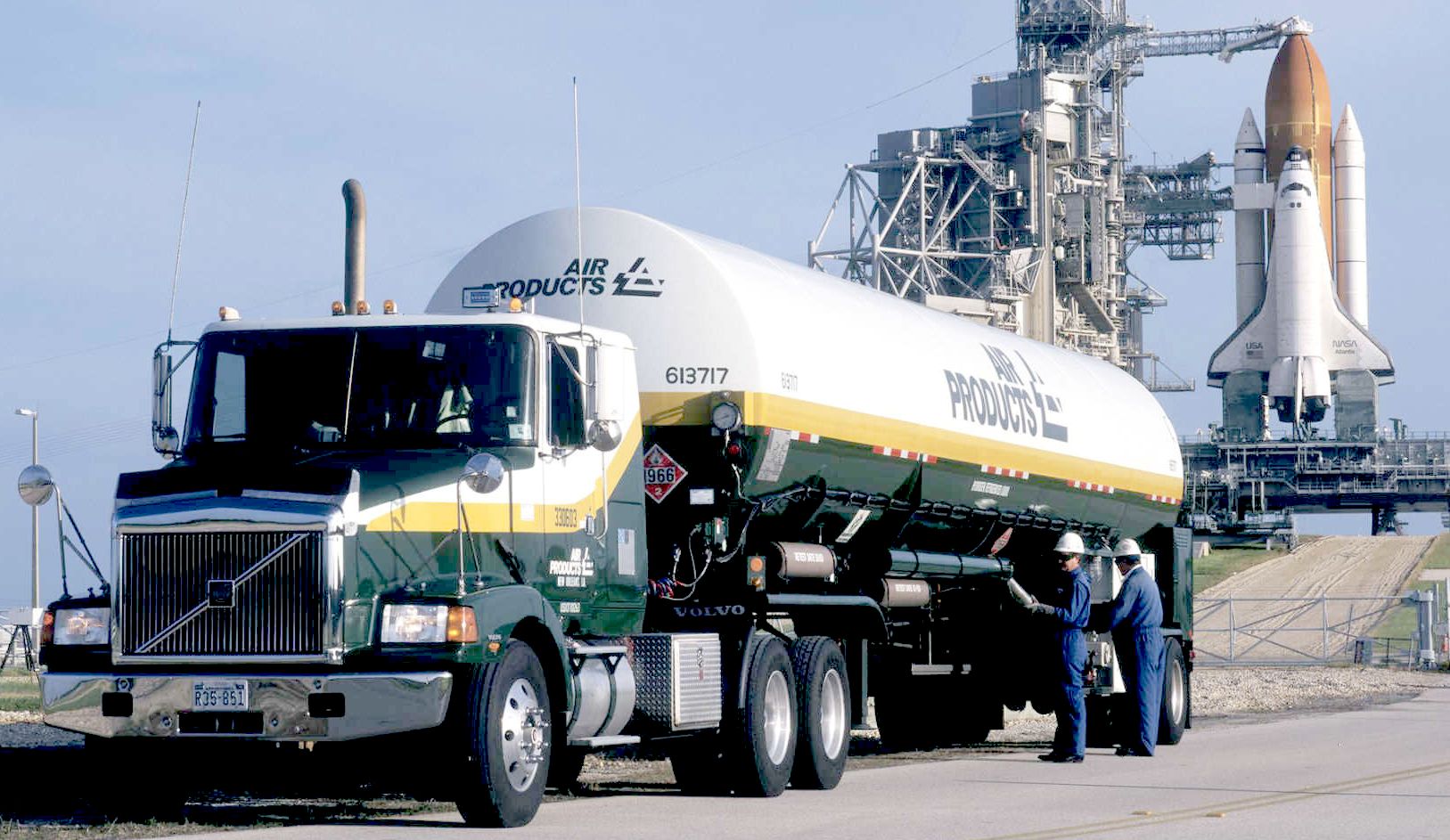
TRUCKING
INFRASTRUCTURE
- Bunkering for ships began with coal, then heavy diesel oil. With the
pollution scare, Liquid Natural Gas was partially introduced as a
cleaner alternative. But with the IMO ramping up clean air targets for
2035 and 2050, there is now a mad rush to develop alternative fuels to
keep international trade alive.
THE LARGEST CRYOGENIC FUEL TANK
NASA’s agency wide goal is to send human astronauts to Mars by the 2030s with SLS and Orion.
Standing more than 130 feet tall, the liquid hydrogen tank is the largest cryogenic fuel tank for a rocket in the world, according to NASA, measuring also 27.6 feet (8.4 m) in diameter.
The SLS core stage stands some 212 feet tall.
The liquid hydrogen (LH2) fuel tank in the Vertical Assembly Center (VAC) welder at NASA’s Michoud Assembly Facility
(MAF) in New Orleans. The VAC is the world’s largest welder.
SLS is the most powerful booster the world has even seen and one day soon will propel NASA astronauts in the agency’s Orion crew capsule on exciting missions of exploration to deep space destinations including the Moon, Asteroids and Mars – venturing further out than humans ever have before!
The LH2 and LOX tanks sit on top of one another inside the SLS outer skin. Together the hold over 733,000 gallons of propellant.
The SLS core stage is comprised of five major structures: the forward skirt, the liquid oxygen tank (LOX), the
inter-tank, the liquid hydrogen tank (LH2) and the engine section.
The SLS core, or first stage, is mostly comprised of the liquid hydrogen and liquid oxygen cryogenic fuel storage tanks which store the rocket propellants at super chilled temperatures. Boeing is the prime contractor for the SLS core stage.
The LH2 and LOX tanks feed the cryogenic propellants into the first stage engine propulsion section which is powered by a quartet of RS-25 engines – modified space shuttle main engines
(SSMEs) – and a pair of enhanced five segment solid rocket boosters (SRBs) also derived from the shuttles four segment boosters.
The vehicle’s four RS-25 engines will produce a total of 2 million pounds of thrust.
The tanks are assembled by joining previously formed dome, ring and barrel components together in the Vertical Assembly Center by a process known as friction stir welding. The rings connect and provide stiffness between the domes and barrels.
The LH2 tank is the largest major part of the SLS core stage. It holds 537,000 gallons of super chilled liquid hydrogen. It is comprised of 5 barrels, 2 domes, and 2 rings.
The LOX tank holds 196,000 pounds of liquid oxygen. It is assembled from 2 barrels, 2 domes, and 2 rings and measures over 50 feet long.
The maiden test flight of the SLS/Orion was targeted for November 2018 and
to be configured in its initial 70-metric-ton (77-ton) Block 1 configuration with a liftoff thrust of 8.4 million pounds – more powerful than NASA’s Saturn V moon landing rocket.
Although the SLS-1 flight in 2018 was un-crewed, NASA plans to launch astronauts on the SLS-2/EM-2 mission slated for the 2021 to 2023 timeframe.
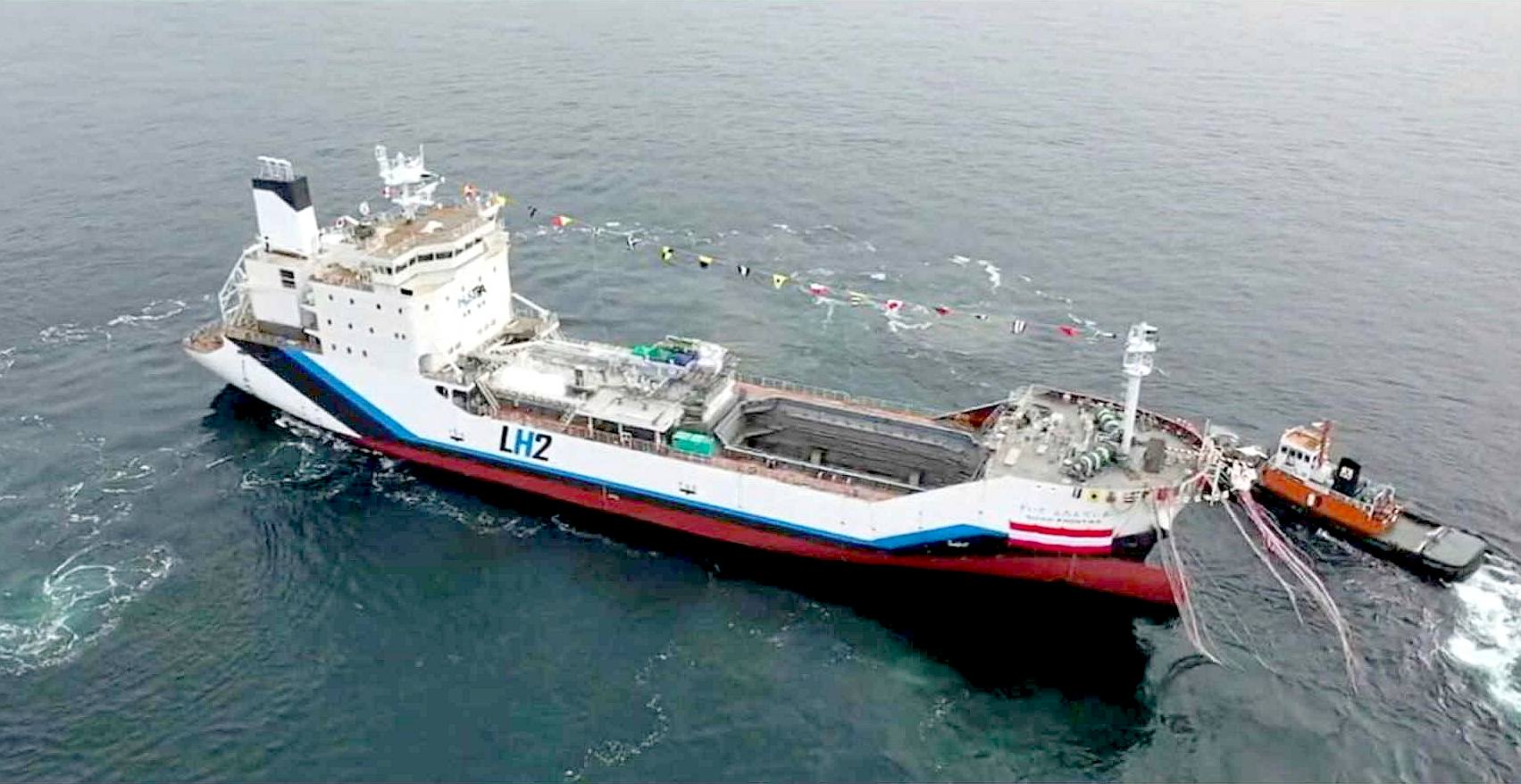
JAPAN LAUNCH WORLD'S FIRST LH2
CARRIER SUISO FRONTIER: The world’s first liquefied hydrogen carrier, built to ship large quantities cryogenically frozen H2 internationally, was launched by Kawasaki Heavy Industries
(KHI) in December 2019.
The Suiso Frontier (‘suiso’ means ‘hydrogen’ in Japanese) will play a key role in the Shell-backed HySTRA demonstration project (CO2-free Hydrogen Energy Supply-Chain Technology Research Association), which will see large quantities of H2 produced from
brown coal in Australia and then shipped 9,000km to the city of Kobe in Japan.
The vessel’s vacuum-insulated hydrogen storage tank will be able to transport 1,250 square metres of liquefied hydrogen (LH2) at temperatures of minus 253°C. The liquefaction process reduces the volume of hydrogen gas by a factor of
800, without even more expensive high pressure
cylinders.
|