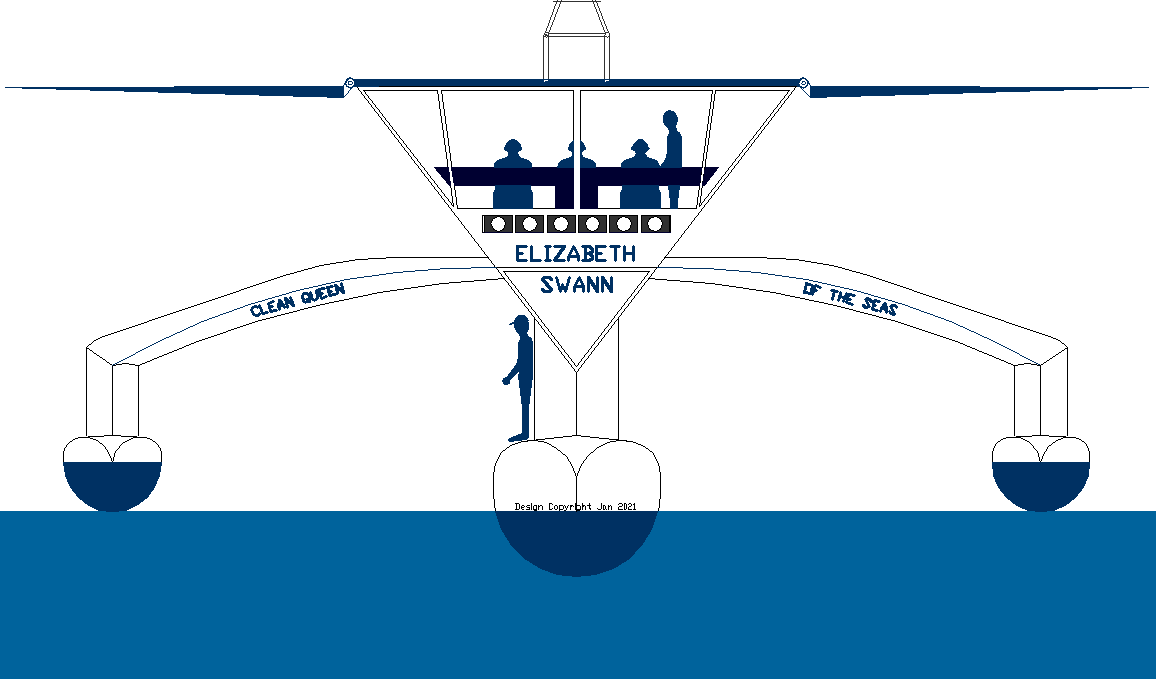
NEW
BOY ON THE BLOCK - In this CAD end elevation, it is possible to see how the simple trimaran hull design lends itself
to experimental use of liquid ammonia in the quest for zero emission waterborne
transport. But like
all technical challenges, until somebody does it, the trophy remains up for
grabs. Nobody has yet crossed a major ocean on ammonia as a stored fuel.
Unsurprisingly, there are manifold technical challenges, yet to be overcome.
This is not off the shelf technology just yet.
Ammonia is now one of the main fuels being considered by the maritime sector to enable the shipping industry to meet new CO2 reduction targets proposed by 2030 and 2050.
See Horizon
Europe: HORIZON-CL5-2021-D5-01-14
June-September 2021 under the ZEWT
partnership.
The raw energy density of liquid ammonia is 11.5 MJ/L, is about a third that of
diesel.
Hence, the space required for fuel storage is typically larger and the material for tanks needs careful selection.
Compared to hydrogen as a fuel, ammonia is more energy efficient, and could be produced, stored, and delivered at a much lower cost than
hydrogen which must be kept compressed or as a
cryogenic
liquid.
LARGE
TANKS
The
unique design of the Elizabeth Swann's hulls gives us the opportunity to
incorporate substantial ammonia storage tanks for use in fuel
cells, or even
as a demonstrator for marine engines, by way of a hybrid electric
generator or smaller backup system.
We
are looking for a good compromise, reduced weight, at a sensible price,
while still offering the storage capacity for blue water voyages and for
use as a medium size ferry.
To
be a truly practical long-range cruiser, we need to store enough ammonia to
cross the Atlantic
or Pacific oceans, with a realistic reserve. We are thus aiming for a range of 4,000+ nautical
miles in all design guises.
As
and when ammonia
technology improves and there is a support infrastructure, the same tanks used for hydrogen storage, could be
used to store ammonia in many of its forms, as a potential range
improver. It is not practical to produce ammonia onboard.
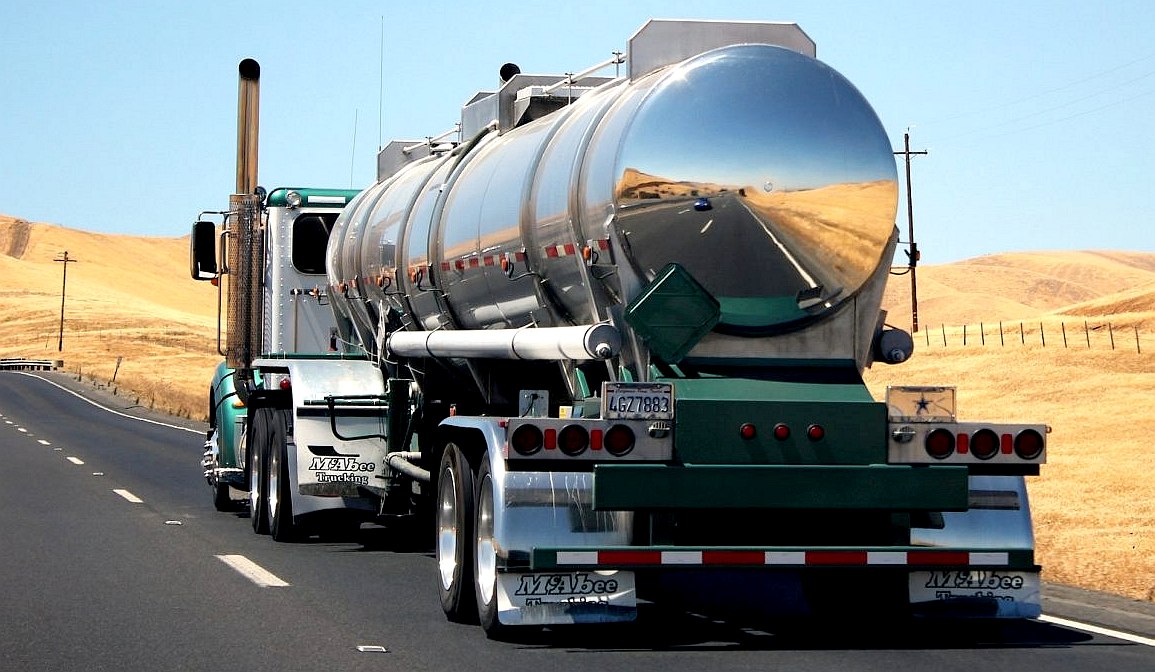
TUBE
TRAILER - Nice rig! Trucks can be used to transport ammonia, as can
railways.
FILLING
THE TANKS UP
As
we write there are no bunkering facilities for ammonia. There is a long
road ahead, if confidence is to reach a point where cargo ships are
converted. Though, obstacles are only slightly more than with hydrogen,
hydrogen is the fuel of choice for land vehicles. Making it more likely
that and infrastructure spreads to the dockside.
In October 2020, the
IMO did not reach an agreement around a
CO2 reduction roadmap for shipping. However, the EU Parliament has voted to include shipping into its Emission Trading Scheme (ETS) from 2022 onwards.
A
BIT ABOUT AMMONIA
Ammonia is a compound of nitrogen and hydrogen with the formula NH3. Ammonia is a stable binary hydride, and the simplest pnictogen hydride,
and a colourless gas with a distinct pungent smell.
Ammonia is both caustic and hazardous in its concentrated form. It is classified as an extremely hazardous substance in the United States, and is subject to strict reporting requirements by facilities which produce, store, or use it in significant quantities.
Industrial ammonia is sold either as ammonia liquor (usually 28% ammonia in
water) or as pressurized or refrigerated anhydrous liquid ammonia transported in tank cars or
cylinders.
Ammonia does not burn readily or sustain combustion, except under narrow fuel-to-air mixtures of 15–25% air. When mixed with oxygen, it burns with a pale yellowish-green flame.
Two fuels contending for the lead alternative fuel are hydrogen and ammonia.
While hydrogen has the advantage of high energy density (on a mass basis), the large storage volumes required, and limited existing infrastructure are considered stumbling blocks in the
'hydrogen as fuel economy.' One solution to this hurdle is to consider a hydrogen carrier, such as ammonia, for the transportation and storage of the fuel and crack it back to hydrogen at the user.
If asked what is the better fuel – ammonia as a stand-alone fuel or hydrogen from cracked ammonia? At the moment, there is not a clear-cut answer to that question.
Utilization of ammonia for marine fuel has been more aggressively researched since 2007. In fact, fuel system developers such as Alfa Laval and engine developers such as Japan Engine Corporation have announced plans to include ammonia in their offerings.[2] Furthermore,
MAN Energy has announced efforts to produce ammonia driven marine operations.[3]
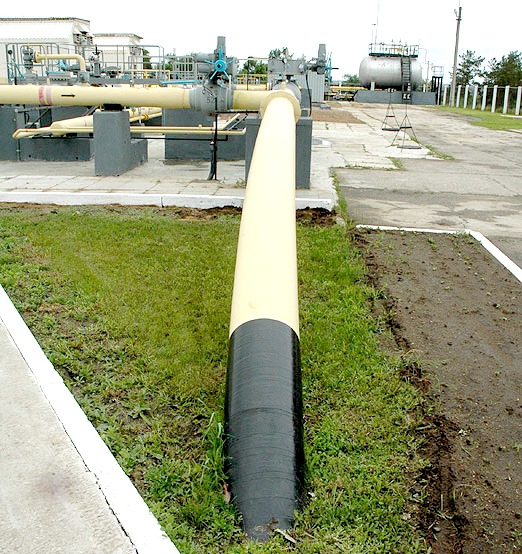
INFRASTRUCTURE -
Delivered via train and pipeline
INTERNAL COMBUSTION ENGINES
Recent studies have shown that efficient and stable combustion of ammonia can be achieved using swirl combustors, thereby rekindling research interest in ammonia as a fuel for thermal power production.
Ammonia engines or ammonia motors, using ammonia as a working fluid, have been proposed and occasionally used. The principle is similar to that used in a fireless locomotive, but with ammonia as the working fluid, instead of steam or compressed air. Ammonia engines were used experimentally in the 19th century by Goldsworthy Gurney in the UK and the St. Charles Avenue Streetcar line in New Orleans in the 1870s and 1880s, and during World War II ammonia was used to power buses in Belgium.
Its high octane rating of 120 and low flame temperature allows the use of high compression ratios without a penalty of high
NOx production. Since ammonia contains no carbon, its combustion cannot produce carbon dioxide, carbon monoxide, hydrocarbons, or soot. Nox being the snag for marine applications.
Ammonia production currently creates 1.8% of global CO2 emissions, a 2020 Royal Society report claims that "green" ammonia can be produced by using low-carbon hydrogen
(blue hydrogen and
green
hydrogen). Total decarbonization of ammonia production and the accomplishment of net-zero targets are possible by 2050.
In 1981, a Canadian company converted a 1981 Chevrolet Impala to operate using ammonia as fuel. In 2007, a University of Michigan pickup powered by ammonia drove from Detroit to San Francisco as part of a demonstration, requiring only one fill-up in Wyoming.

Rocket engines have also been fueled by ammonia. The Reaction Motors XLR99 rocket engine that powered the X-15 hypersonic research aircraft used liquid ammonia. Although not as powerful as other fuels, it left no soot in the reusable rocket engine, and its density approximately matches the density of the oxidizer, liquid
oxygen, which simplified the aircraft's design.
In early August 2018, scientists from Australia's Commonwealth Scientific and Industrial Research Organisation (CSIRO) announced the success of developing a process to release hydrogen from ammonia and harvest that at ultra-high purity as a fuel for cars. This uses a special membrane. Two demonstration fuel cell vehicles have the technology, a
Hyundai Nexo and
Toyota Mirai.
In 2020, Saudi Arabia shipped forty metric tons of liquid "blue ammonia" to Japan for use as a fuel. It was produced as a by-product by petrochemical industries, and can be burned without giving off greenhouse gases. Its energy density by volume is nearly double that of liquid hydrogen. If the process of creating it can be scaled up via purely renewable resources, producing green ammonia, it could make a major difference in avoiding climate change. The company ACWA Power and the city of Neom have announced the construction of a green hydrogen and ammonia plant in 2020.
Green ammonia is considered as a potential fuel for future container ships. In 2020 the companies DSME and MAN Energy Solutions announced the construction of an ammonia-based ship, DSME plans to commercialize it by 2025.
ICE
PROBLEMS
Higher compression ratios are required for ammonia, often resulting in a dual fuel injection (e.g. ammonia + diesel, ammonia + hydrogen) to keep the compression ratio modest. In addition, dual fuel applications have been considered to improve flame stability and balance CO and NOx emissions.
the second challenge faced by ammonia as fuel is NOx emissions. A clear understanding of an engine’s mode of operation is highly important to mitigating NOx and unburnt ammonia in the exhaust gas. For example, some studies have shown NOx emissions exceeding 1000 ppm for engine operation on ammonia. Research has progressed to show that these high NOx emissions can be significantly reduced with engine design and systematic tuning. More specifically, studies have shown the importance of combustor inlet temperature, injection port location, fuel blend, and air injection rate on NOx and ammonia
emissions.
Consensus prevails about the technical challenges that an ammonia engine must overcome. The Caterpillar Corporation put it succinctly in their 2008 patent application that covers a “power system having an ammonia-fueled engine”: “When ammonia is combusted, the combustion produces a flame with a relatively low propagation speed.
This low combustion rate of ammonia causes combustion to be inconsistent under low engine load and/or high engine speed operating conditions. Most existing combustion engines that use ammonia as engine fuel typically require a combustion promoter (i.e., a second fuel such as
gasoline, hydrogen, diesel, etc.) for ignition, operation at low engine loads and/or high engine speed.”
One option is to use a liquid combustion promoter. However, as the patent subsequently notes, this approach “generally requires dual fuel storage systems, dual delivery systems, and dual injection systems, thus adding additional weight, complexity, and cost to the engine system.”
The second option is to use hydrogen as the combustion promoter. A promising variant of this approach is to place an on-board reformer between the fuel tank and the engine. The reformer can be set up to “crack” enough of the ammonia into hydrogen and nitrogen to support viable combustion.
Caterlillar's patent describes one more challenge: “The requirement for the combustion promoter fuel fluctuates with varying engine loads and engine speed, which can cause control issues.” This means that cracking a fixed proportion of the ammonia (or a proportion that varies simply with the rate of fuel flow) is unlikely to produce good engine function.
In 2016, development was distributed across three camps:
1. There are the carbon-based dual-fuel players working with spark-ignition systems. These include Bigas International and the SAVIA coalition of Italy; the Green Transportation Technology Group at the Korean Institute for Energy Research; and the ammonia research group at Xiamen University in China.
2. There are the carbon-based dual-fuel players working with compression-ignition systems. These include Sturman Industries (whose ALL-ternative engine was recently profiled by AmmoniaEnergy); Hydrofuel Inc. of Canada; and Song-Charng Kong’s program at Iowa State University. Caterpillar’s patent implies the use of a secondary fuel that is not hydrogen, but is silent on which ignition method might be employed.
3. There are the players who are using hydrogen as the combustion promoter. These include
Toyota’s Central R&D Labs; and the
Hydrogen Engine Center of Iowa in the U.S.
FUEL
CELLS
Until recently, use of ammonia in fuel cells has been limited due to the tendency of ammonia to dissolve the cell membrane. Advances in solid-oxide fuel cells (SOFC) and polymer electrolyte membrane fuel cells (PEMFC) are proving ammonia as a fuel for fuel cells can be a viable
option.
Ammonia can
be used as a source of hydrogen for acid fuel cells if the
un-reacted ammonia can be removed. Ruthenium and platinum catalysts were found to be the most active, whereas supported Ni catalysts were the less active.
There is the opportunity to convert ammonia back to hydrogen, where it can be used to power hydrogen
fuel cells or it may be used directly within high-temperature solid oxide direct ammonia fuel cells to provide efficient power sources that do not emit greenhouse gases.
The conversion of ammonia to hydrogen via the sodium amide process, either for combustion or as fuel for a proton exchange membrane fuel cell, is possible. Conversion to hydrogen would allow the storage of hydrogen at nearly 18 wt% compared to ≈5% for gaseous hydrogen under pressure.
The production of hydrogen from cracked ammonia is straight forward, and commonly done for industrial applications, such as metal nitriding applications, using heterogeneous catalysis. Ammonia is passed through a heater and then passed over a catalyst bed to use oxidation of ammonia (ammonia decomposition into nitrogen and water) to supplement the endothermic decomposition of ammonia into hydrogen and nitrogen. Existing cracker technology is readily available in the 1-2 ton/day
range from companies such as Lindberg/MPH, CI Hayes, Koyo Thermo, and Sergeant & Wilbur, Inc. Small scale cracking applications have been proposed but are not commercially
available.
PRODUCTION
Ammonia is globally one of the most industrially produced chemicals, with yearly production of over 150 million tons and an even further increased production is expected in the coming years. Ammonia is a crucial chemical in fertiliser production and results from combining hydrogen with nitrogen from air in an industrial process called the Haber–Bosch process. This is one of the oldest processes in the chemical industry and the first large scale plant for this process was constructed in Oppau, Germany in 1913 and was able to produce 30 tons of ammonia per
day.
The 60 MW Rjukan dam in Telemark, Norway, produced ammonia for many years from 1913, providing fertilizer for much of Europe.
The Haber–Bosch reaction is a catalytic exothermic chemical reaction that takes place at increased temperatures (300–500 °C) and pressure (15–20
MPa).
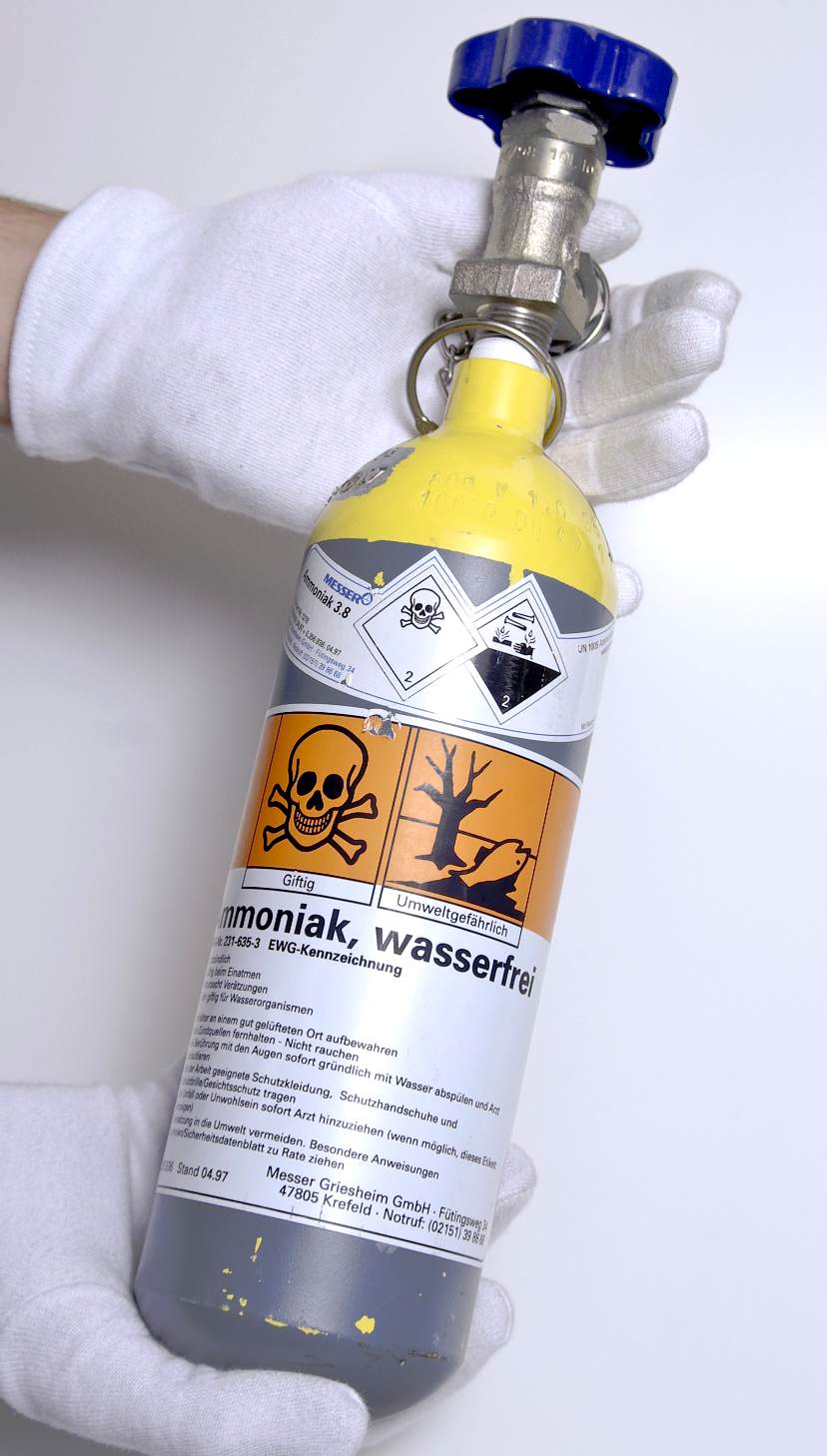
REFERENCES
[1] A review of ammonia as a compression ignition engine fuel. Dimitriou, Pavlos and Javaid, Rahat. International Journal of Hydrogen Energy. 15(2020)7098-7118.
[2] A Preliminary Study on an Alternative Ship Propulsion System Fuel by Ammonia: Environmental and Economic Assessments. Kim, Kyunghwa et al. Journal of Marine Science and Engineering. March 7, 2020.
[3] The Potential Role of Ammonia as Marine Fuel—Based on Energy Systems Modeling and Multi-Criteria Decision Analysis. Hansson, Julie et al. Sustainability, April 17, 2020.
[4] Ammonia for Power. Valera-Medina, A, & et.al. Progress in Energy and Combustion Science (2018), 63-102.
[5] Ammonia, Methane, and Hydrogen for Gas turbines. Valera-Medina, A., et. Al. Energy Procedia (2015), 118-125.
[6] Performance of Ammonia-Natural Gas Co-Fired Gas Turbine for Power Generation. Ito, Shintaro. 2018 AiChE Annual Meeting.
[7] American Energy Conference 2020, Panel 1. Presentation from Starfire Energy.
[8] Science and Technology of Ammonia Combustion. Kobayahi, Hideaki et al. Proceeds of the Combustion Institute 37(2019),109-133.
[9] Power to Gas: Hydrogen for Power Generation. Fuel Flexible Gas Turbines as Enablers for a Low or Reduced Carbon Energy Ecosystem. GEA3861. February 2019.
[10] Ammonia to Green Hydrogen Project: Feasibility Study. Siemens, ENGIE, Ecuity, and Science & Technology Facilities Council, April 2020.
[11] Ammonia as an Alternative Energy Storage Medium for Hydrogen fuel Cells: Scientific and Technical Review for Near-Term Stationary Power Demonstration Projects, Final Report. Lipman, Tim and Shah, Nihar. Research Report UCB-ITS-TSRC-RR-2007-5. November 2007.
[12] Estimating SCR Installation Costs, Power (2006).
[13] Selective Catalytic Reduction, Chapter 2. Sorrels, John. May 2016.
[14] Cost Report and Guidance for Air Pollution Regulations. EPA, url: https://www.epa.gov/economic-and-cost-analysis-air-pollution-regulations/cost-reports-and-guidance-air-pollution
[15] Lindberg/MPH Model 16-RO-150-HYAM; budgetar
[16]
https://pubs.rsc.org/en/content/articlehtml/2021/ee/d0ee01545h
[17]
https://pubs.rsc.org/en/content/articlehtml/2021/ta/d0ta08810b
|